
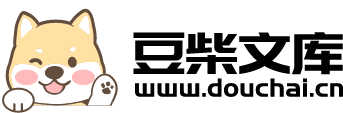
一种熔模精密铸造方法.pdf
梅雪****67
在线预览结束,喜欢就下载吧,查找使用更方便
相关资料
一种熔模精密铸造方法.pdf
本发明公开了一种熔模精密铸造方法,主要包括涂料制壳、脱蜡、焙烧、浇注、等步骤,根据铸件易出现疏松缺陷的部位结构,制作一冷却部件,再根据冷却部件的轮廓尺寸制作与之相同的冷却部件蜡模,然后将冷却部件蜡模设置在铸件蜡模的相应位置上;每涂一层料后,将冷却部件蜡模外表面的涂层擦掉,以便在脱腊和焙烧步骤后,在型壳上形成一个具有放置冷却部件的空腔;将冷却部件放置在空腔中并固定,本发明巧妙的避开了冷却部件随着型壳高温焙烧,防止了冷却部件因高温焙烧产生的外表面氧化和内部结构变化,提高了冷却部件的冷效果,可有效防止铸件缩孔、
一种熔模精密铸造型壳的制造方法.pdf
一种新型熔模精密铸造工艺,包括:(1)涂料的配制,(2)风干硬化顺,(3)硬化液的配,(4)硬化时间,(5)风干时间的确定。其特征在于:包括上述工艺参数组合成一种新型熔模精密铸造工艺。本发明提供了一种新型熔模精密铸造工艺,具有提高型壳强度,降低铸件外跑火质量缺陷;缩短风干硬化时间,提高生产工效,硬化风干充分,提高表面质量,降低废品率;环境因素(温度、湿度)影响小,避免批量废品发生等优点。可满足生产形状复杂、精度及表面质量要求高、难以进行其它加工的中大型复杂零件,如涡轮发动机的叶片等。适合在熔模精密铸造行业
一种低压熔模精密铸造工艺.pdf
本发明公开了一种低压熔模精密铸造工艺,造型钢板上叠置砂箱,组合型壳置于造型钢板中心孔中,用石棉绳将缝隙塞实,再在浇口杯外周采用粘土砂固定,用干砂将砂箱填满并刮平;将造型钢板吊装放置在吊装钢板之上且固定,再将吊装钢板吊放并固定在低压铸造机工作台上,在砂箱顶部覆盖压紧钢板并压紧;将保温炉推进至工作位置并升起,直至升液管的上端口与浇口杯型壳的下端口对接且两者之间实现密封;向保温炉的气相空间通入压缩气体,保温炉底部的金属液沿升液管上升,进入组合型壳的型腔内,薄壁产品型腔内的金属液在压力下凝固后,进行放气,金属液回
一种精密铸造电熔砖砂模的制备方法.pdf
本发明涉及一种精密铸造电熔砖砂模的制备方法,技术方案是,包括以下步骤:A、用木板制作砂型模具;B、制作砂型填充料,砂型材料是由白刚玉、硅酸乙酯水解液、氢氧化钙、双氧水、玻璃纤维和乙醇制成;C、将砂型填充料浇注到砂型模具的砂型成型空间,浇注后,在砂型表面铺盖一层塑料膜,防止乙醇挥发;5‑15分钟后起模,起模后,用明火点燃砂型,砂型内乙醇燃烧,同时燃烧砂型内的有机物质,使砂型快速形成达到强度,即得精密铸造电熔砖砂模;通过本发明砂模生产的电熔砖无需研磨加工,可直接使用,表层致密、耐玻璃液高温侵蚀,延长了玻璃窑炉
一种用于熔模精密铸造的蜡模制备方法.pdf
本发明公开了一种用于熔模精密铸造的蜡模制备方法,包括以下步骤,(1)模具合模(2)配制蜡料:将蜡料加入到压蜡机的保温炉中,将温度升高至90~100℃,待蜡料完全融化后,边搅拌边加入粒度6~14μm、含量3~5wt%的碳化硅颗粒,加入完成后静置20~30min,在压蜡机冷却槽中注入20~25℃的冷却水,将蜡温降至55~60℃待用;(3)压制蜡模:将压蜡机中的蜡料通过注蜡枪在0.3~0.5MPa的压力下注入模具型腔中,待排气孔中有蜡排出时,停止注蜡,然后开启模具水冷系统,流量控制在5~8L/min,当测温热电