
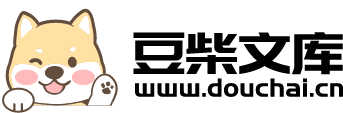
薄壁外齿轮内孔的加工方法.pdf
依波****bc
在线预览结束,喜欢就下载吧,查找使用更方便
相关资料
薄壁外齿轮内孔的加工方法.pdf
本发明公开一种薄壁外齿轮内孔的加工方法,采取新工艺和夹具解决上述问题。本发明采取的加工步骤:锻造、粗车、调质、半精车、半精车、精车、滚齿、去应力退火、平磨端面、磨内孔、磨齿、齿面氮化;粗车给前半精车留量1.5mm,前半精车给后半精车留量为0.7mm,后半精车给精车留量为0.3mm,分三次车削;磨内孔采用专用夹具,用定位棒使夹具体与工件齿轮同心,之后用夹具体使工件齿轮以一个端面及齿顶定位,再用压板压紧工件齿轮,磨内孔;圆度可以达到0.02mm,直线度可以达到0.003mm;齿面氮化变形后内孔圆度0.08mm
人字齿轮内孔键槽对称加工工装及加工方法.pdf
人字齿轮内孔键槽对称加工工装及加工方法,人字齿轮内孔键槽对称加工工装,包括工装本体,所述工装本体沿中心线方向两端分别设有定位孔和齿槽定位孔,沿中心线方向定位孔左右两侧的工装本体上分别设有基准键槽,工装本体设有齿槽定位孔的一端侧壁上自上而下设有若干螺纹孔,螺纹孔中心位于侧壁中心线上,定位孔上设有定位套,齿槽定位孔上设有齿槽定位轴,螺纹孔上设有调整螺钉,它具有结构设计合理,利用人字齿轮分度圆端面齿廓齿面及内孔定位,靠工装上键槽侧面控制对称来保证人字齿端面齿槽中心、内孔键槽中心与孔中心线必须在同一直线上的技术要
一种加工齿轮内孔的定位方法.docx
一种加工齿轮内孔的定位方法论文题目:一种加工齿轮内孔的定位方法摘要:齿轮是机械传动中常用的零部件之一,其内孔的加工定位对于齿轮的性能和传动精度具有重要影响。本论文提出了一种新的加工齿轮内孔的定位方法,通过数控机床和传感器的协同工作,实现对齿轮内孔位置和形状的高精度定位与加工。该方法具有定位精度高、加工效率高、操作简单等优点,适用于各种规格和精度要求的齿轮内孔加工。关键词:齿轮加工;内孔定位;数控机床;传感器1.引言齿轮是机械传动中常用的零部件之一,广泛应用于各种机械设备中。齿轮的内孔作为安装在轴上传动的关
薄壁管件内孔外圆同心度高精度加工工艺.pdf
本发明公开了一种薄壁管件内孔外圆同心度高精度加工工艺。管料进行热处理调质;将管料在车床上进行粗加工,加工外圆和内孔;将管件在加工中心内加工管件造形,以管件外圆为精准将管件造形加工到位;将管件在数控车床上对管件外圆和内孔进行精加工;将管件放入时效炉中释放应力;将管件放在数控车床上对内孔进行加工,采用包爪固定管件,包爪的包覆面将管件外表面完全包覆,然后数控车床对管件内孔加工到位;将外圆加工芯棒插入管件内孔,外圆加工芯棒在管件造型部位和管件末端与管件内孔壁接触,管件内孔其余部分与外圆加工芯棒不接触,通过两顶尖夹
内齿轮加工方法及内齿轮加工机.pdf
本发明的目的在于提供一种能够在使用鼓形螺旋状砂轮对内齿轮的齿形实施磨削加工时修正齿形形状误差从而实现高精度的齿形磨削加工的内齿轮加工方法及内齿轮加工机。因此,作为内齿轮磨削盘(内齿轮加工机)的齿形形状误差修正机构发挥作用的NC装置(31)构成为,通过修正径向位置、砂轮横向位置、砂轮回旋角、螺旋运动而使计测到的工件(W)(内齿轮)的齿面的压力角误差(ΔfaL、ΔfaR)减少,通过修正螺旋运动而使计测到的工件(W)的齿面的齿向误差(ΔL)减少,通过修正径向位置、砂轮横向位置、螺旋运动而使计测到的工件(W)的齿