
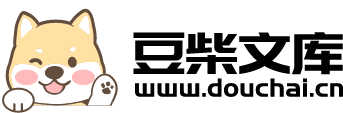
制动盘及其制造方法.pdf
爱欢****23
亲,该文档总共17页,到这已经超出免费预览范围,如果喜欢就直接下载吧~
相关资料
制动盘及其制造方法.pdf
为了重量轻便且能够提高刚性,并通过改善盘板与轮毂的结合结构来使重量最小化且能够提高生产效率,提供一种制动盘制造方法,所述制动盘包括:盘板,提供摩擦面并在中央形成有孔;轮毂,结合于所述盘板的中央形成的孔,所述方法包括:准备盘板的步骤;准备平板形态的轮毂的步骤;使平板形态的轮毂位于盘板一面的步骤;将所述盘板和轮毂以过盈配合方式进行接合的步骤。
制动盘及其制造方法.pdf
本发明涉及一种用于制造由基体(1)构成的制动盘的方法,该基体具有摩擦环表面(2)。该方法包括提供基体(1)以及通过将电子射束(5)对准摩擦环表面(2)而对摩擦环表面(2)进行粗糙化处理的步骤,其中在摩擦环表面(2)中在每mm2的摩擦环表面(2)上产生规定数量的凹处(3)。凹处(3)彼此之间的布置结构在此是预先设定的,且每个凹处(3)都具有预先设定的深度和形状。然后在不进行蚀刻步骤的情况下涂覆摩擦环表面涂层(4)。此外公开了一种相应的制动盘。
制动盘的制造方法以及制动盘.pdf
本发明提供能够提高前后轮的波形盘的成品率的制动盘的制造方法以及制动盘。所述制动盘的制造方法是,从板状部件上切裁盘片部件(131)而制造制动盘(105、111),在该方法中,通过对一张盘片部件(131)在径向的中间部以圆周方向波形切裁而制造出外侧盘(105)和内侧盘(111),将向外侧盘(105)的径向内侧伸出的波形部作为向轮部安装的安装部(117),将向内侧盘(111)的径向外侧伸出的波形部作为蹄片夹持部(125)。
制动盘的制造方法、制动盘及盘式制动器.pdf
本发明提供了一种制动盘的制造方法、制动盘及盘式制动器。制动盘的制造方法包括:将制动盘的摩擦环和盘帽嵌套设置;将摩擦环和盘帽放置到焊接固定夹具上;对摩擦环和盘帽进行焊接。本发明解决了现有技术中制动盘的制造工艺复杂的问题。
双金属制动盘及其制造方法.pdf
本发明涉及一种双金属制动盘及其制造方法。该制动盘包括两摩擦片,且两摩擦片之间留有通风空间;两摩擦片之间还设有一组导流叶片,导流叶片将通风空间分隔成一组通风腔;还包括散热加强件;散热加强件包括一组分别位于通风腔内的第一散热件、以及位于两摩擦片内环边缘处的第二散热件;第一散热件与导流叶片及两摩擦片相贴或经铸造固连,第二散热件与两摩擦片的内环边缘分别相贴或经铸造固连;第二散热件具有一组分别与对应通风腔连通的通孔。本发明制动盘保留现有空心通风式制动盘的所有优点,且因其独特设计,使用寿命长,散热好,重量轻,机械性能