
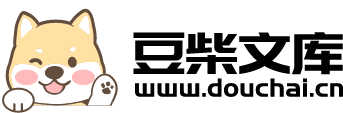
一种基于金属压印的载板填孔工艺.pdf
一条****贺6
在线预览结束,喜欢就下载吧,查找使用更方便
相关资料
一种基于金属压印的载板填孔工艺.pdf
本发明公开一种基于金属压印的载板填孔工艺,包括以下步骤:(1)对待填孔的载板表面进行预处理,使载板表面与金属不具有结合力;(2)将填充基材覆盖在载板表面;(3)对填充基材施加垂直于载板表面的下压力,使得填充基材发生形变并压入载板上的通孔或盲孔中;(4)对载板和覆盖在载板表面的填充基材进行分离处理,去除载板表面的填充基材,并让载板上通孔或盲孔中的金属仍然保留在内部,完成载板的填孔加工。本发明实现载板的快速填孔,以便实现通孔、盲孔的互连结构,并且填充效果好,有利于提高通孔、盲孔的导电、导热性能。
载板填孔工艺的填充基材选型方法及载板填孔工艺.pdf
本发明公开一种载板填孔工艺的填充基材选型方法及载板填孔工艺,其中的填充基材选型方法,包括以下步骤:(1)确定载板上通孔或盲孔的尺寸及所需性能情况;(2)选择合适的填充基材类型;(3)选择填充基材的粒径大小;其中,填充基材的粒径大小选择如下:(a)小粒填充,D=0.001~0.2d(b)串式填充,D=0.5d~2d(c)单粒整体填充,D=0.5(1.5d2h)0.5~2(1.5d2h)0.5;其中,上述式中D为填充料的直径,d为载板上通孔或盲孔的直径,h为载板上通孔或盲孔的深度。本发明的填充基材选型方法,为
一种HDI载板埋孔填埋工艺及其使用方法.pdf
本发明涉及C25D3/38领域,具体为一种HDI载板埋孔填埋工艺及其应用,通过设计黑化和棕化处理步骤,层压步骤,钻孔步骤,除油步骤,高压水冲洗步骤,二次水洗步骤,孔金属处理步骤,塞孔步骤和电镀步骤,保证HDI载板盲埋孔填埋的稳定性,解决现有技术中由于塞孔不完全、树脂和铜层容易分离导致HDI载板质量降低的问题,有效消除孔内气泡,满足额外的高导热性的需求,防止元器件增多容易过载,保证HDI载板的质量和使用寿命,通过该工艺处理后的HDI载板尤其适用于手机、电子手表领域。
用于HDI板和载板的盲孔填孔电镀铜溶液.pdf
本发明公开了一种用于HDI板和载板的盲孔填孔电镀铜溶液,电镀铜溶液包括以下浓度的组分:五水硫酸铜:150‑200g/L;硫酸(98%):40‑80g/L;氯离子:30‑70mg/L;光亮剂:0.5‑4mg/L;润湿剂:200‑500mg/L;整平剂:5‑30mg/L;新添加剂:30‑100mg/L;去离子水:余量;将上述的组分按照浓度混合后形成该电镀铜溶液,该电镀铜溶液电镀时先将电镀槽用Dummy片电解至2AH/L,再用电流密度在1‑3A/dm
一种柔性线路板盲孔镀铜填孔工艺.pdf
本发明公开了一种柔性线路板盲孔镀铜填孔工艺,包括如下步骤:S1.黑影;S2.闪镀:整版进行镀铜,镀层厚度为2‑4微米。在盲孔孔内形成良好的导电效果;S3.压膜;S4.曝光;S5.显影;S6.电镀铜:对产品选择性进行填孔镀铜。本发明通过在黑影工序后增加一道闪镀强化孔内膜层的工序,可以有效保证在后续电镀时孔内的导电性良好。本工艺方式对于两面孔深、孔径相差较大的产品,填孔效果良好。