
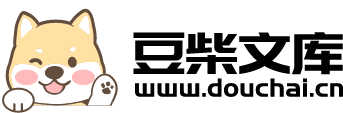
一种降低转炉炉底厚度的方法.pdf
书生****12
在线预览结束,喜欢就下载吧,查找使用更方便
相关资料
一种降低转炉炉底厚度的方法.pdf
本发明公开了一种降低转炉炉底厚度的方法,所述方法包括以下步骤:根据转炉炉底的渣层厚度,在转炉出钢过程中预留能够将所述渣层完全反应掉的钢水;向转炉中滑动吹氧进行吹炼;对转炉中的熔池进行冷却降温,最后倒掉炉渣。本发明的方法不需向炉内重新兑入半钢或铁水等化炉底材料,并有效地利用了出钢时钢水和钢渣的温度,在氧气吹炼过程中也不需造渣,具有操作简单、节奏快、成本低的优点。
降低炼钢转炉炉底的方法.pdf
本发明属于冶金技术领域,尤其针对一种降低炼钢转炉炉底的方法。针对现有转炉冶炼时炉底上涨导致炼钢炉有效容积变小、脱磷效果变差,易喷溅等问题,本发明提供一种降低炼钢转炉炉底的方法,包括以下步骤:每一炉炼钢出钢结束后,测量炉底厚度;当炉底厚度达到新砌炉炉底厚度的90%以上时,下一炉冶炼出钢后留钢转炉公称容量的4~8%,留钢后将转炉摇到零位,并向炉内加入硅铁10~20kg/t钢,顶吹氧气30~60s,倒出钢水和炉渣。本发明通过硅铁在适宜的吹氧条件上反应,消耗炉渣,操作简单,效果显著,具有明显的经济效益。
一种转炉炉底厚度的控制方法.pdf
本申请提供了一种转炉炉底厚度的控制方法,通过改进氧枪喷头参数,在对转炉氧枪改造的基础上合理使用氧压,控制转炉装入量和控制造渣料用量,控制连续喷溅、返干,出现上涨趋势时及时采取降炉底措施,通过调整操作方式及工艺参数缓慢降低炉底,稳定了炉底厚度为650mm‑850mm,避免了转炉炉底上涨,缩短了转炉冶炼周期1min,降低了转炉终渣的全铁含量至14%以下,增加了转炉终渣黏度,提高了转炉生产效率,有利于转炉炉型的维护,提高了转炉寿命。
一种降低转炉炉底高度的方法.pdf
本发明提供一种降低转炉炉底高度的方法,包括如下步骤:(1)将转炉钢水终点碳控制在0.06%以下,终点炉渣TFe控制在15%以上;(2)出钢完毕后,倒出部分炉渣;(3)将氧枪枪位降至氧枪枪头距炉底2100~2300mm之间恒定不变后开氧,氧压控制在0.90~0.96MPa之间,开氧时间控制在50~60s;(4)关氧,提枪;确认氧枪无漏水后将炉渣从炉口倒出。本方法操作简便,对炉底处理效率高,且效果明显;对转炉炉衬熔池、炉帽等部位损害小;炉底上涨后使用本方法能够及时将炉底降至正常范围内,不仅使转炉过程冶炼得以稳
一种转炉炉底厚度测量装置及方法.pdf
本发明提供了一种转炉炉底厚度测量装置及方法,包括底吹供气元件(1)、底吹供气控制系统(3)、供气元件长度检测系统(4)、系统控制器(5);转炉(2)底部有安装底吹供气元件(1)的安装孔,底吹供气控制系统(3)一端通过管线与底吹供气元件(1)相连,另一端与系统控制器(5)相连,供气元件长度检测系统(4)一端通过线缆连接至底吹供气元件(1),另一端与系统控制器(5)相连。本发明适用于任何公称容量的复吹转炉,本装置结构简单,易于实施与维护,能够很容易测得炉底厚度、底吹供气元件的厚度、渣层的厚度,根据测得的厚度对