
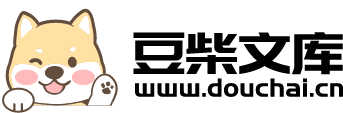
一种转炉钢渣炉内气化脱磷炼钢的方法.pdf
佳晨****ng
在线预览结束,喜欢就下载吧,查找使用更方便
相关资料
一种转炉钢渣炉内气化脱磷炼钢的方法.pdf
本发明涉及一种转炉钢渣炉内气化脱磷炼钢的方法,属冶金技术领域。该方法包括:第一炉冶炼:吹气,开吹的同时向第一炉中加入造渣材料,控制终点炉渣碱度,直至吹炼结束,出钢前加入第一无烟煤,出钢后溅渣,气化脱磷并保留全部钢渣。第二炉冶炼:将造渣材料用量减半,出钢后保留一半炉渣,然后溅渣并保留剩余的钢渣;其余步骤与第一炉冶炼相同。第三炉至第十炉冶炼:将造渣材料用量在第一炉的基础上减少20‑30wt%,出钢后保留一半炉渣,然后溅渣;其余步骤与第一炉冶炼相同。此方法简单,能降低钢渣中磷含量,增加钢渣循环利用次数及降低辅料
一种转炉钢渣炉内循环的脱磷炼钢方法.pdf
本发明涉及一种转炉钢渣炉内循环的脱磷炼钢方法,属冶金技术领域。该方法包括:第一炉冶炼:兑入半钢,吹入氧气,开吹时加入第一造渣材料,控制终点炉渣碱度为3‑4至吹炼结束,出钢后溅渣并保留全部钢渣。第二炉冶炼:将第一造渣材料用量减半;其余同第一炉冶炼。第三炉冶炼:采用双渣留渣方法,脱磷期不加料,调整炉渣碱度为1.5‑2.5,低温脱磷,倒掉部分富磷渣,加入第二造渣材料二次造渣,保留全部钢渣。第四炉冶炼:采用单渣法再次造渣冶炼,出钢后倒掉一半的炉渣,溅渣时加入无烟煤气化脱磷;其余同第二炉冶炼。第五炉至第二十炉冶炼同
一种转炉脱磷炼钢方法.pdf
本发明提供了一种转炉脱磷炼钢方法。所述方法包括步骤:a、向转炉熔池中加入由活性石灰、高镁石灰和复合造渣剂组成的造渣材料,同时通过脱磷氧枪吹氧工艺和惰性气体底吹工艺来吹炼造渣以脱除钢水中的磷,当转炉中的熔池温度为1420~1450℃、炉渣的碱度为2.0~2.5、炉渣中的全铁含量为10~15wt%时,倒出60~80%的炉渣;b、向转炉熔池中加入造渣材料,同时通过普通氧枪吹氧工艺和惰性气体底吹工艺来吹炼造渣以进一步脱除钢水中的磷,当转炉中的熔池温度为1680~1700℃、炉渣的碱度为3.2~4.2、炉渣中的全铁
一种半钢冶炼转炉终渣炉内气化脱磷及循环利用方法.pdf
本发明涉及一种半钢冶炼转炉冶炼终渣炉内气化脱磷的方法,包括:半钢转炉冶炼完毕出钢后,将转炉终渣全部留在炉内;摇正炉体后,由高位料仓向炉内加入定量的SiC粉剂;降枪进入调渣操作,调整枪位及氮流量进行气化脱磷;调渣操作后,快速提升枪位、氮流量至溅渣护炉水平,直接进行溅渣护炉操作;溅渣完毕后,炉渣全部留在炉内,进入下炉次半钢冶炼。本发明借助溅渣护炉期间的良好动力学条件及真空条件,利用SiC作为脱磷剂对终渣进行气化脱磷,一方面提升了气化脱磷率,另一方面脱磷后的酸性产物降低了熔渣碱度,留渣操作后利于下炉次控磷生产。
半钢炼钢转炉炉后脱磷的方法.pdf
本发明属于冶金技术领域,具体涉及一种半钢炼钢转炉炉后脱磷的方法。现有缺乏对半钢炼钢中后期的斡旋效应卷渣进行控制,降低磷含量的方法,本发明提供了一种半钢炼钢转炉炉后脱磷的方法,包括以下步骤:a、120t转炉冶炼,转炉兑入半钢后,开吹的同时向炉内加入活性石灰20~25kg/t钢,高镁石灰30~35kg及酸性复合造渣剂8~12kg/t钢;b、氧枪喷头距熔池金属液面基本枪位1.4~2m,吹炼枪位1.4m~1.8m,开吹枪位2m,拉碳枪位1.4m;c、吹炼结束后,出钢前向转炉加入轻烧白云石8~10kg/t钢和钢渣8