
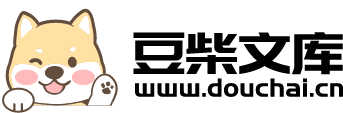
一种石墨烯微球的制备方法及应用.pdf
冬易****娘子
在线预览结束,喜欢就下载吧,查找使用更方便
相关资料
一种石墨烯微球的制备方法及应用.pdf
本发明公开了一种石墨烯微球的制备方法及应用,石墨烯微球制备包括如下步骤:S1)将石墨粉、浓硫酸和硝酸钠混合,超声分散、搅拌均匀制得混合液;S2)向混合液中缓慢加入高锰酸钾,搅拌混合,制得胶体;S3)将乳化剂和有机溶剂混合制得油相溶液,将S2制备的胶体加入到油相溶液中,搅拌混合,制得胶体微球;S4)将胶体微球经过水热处理,清洗、干燥后置于马弗炉中处理,制得石墨烯微球。本发明制备工艺简单,反应条件易于控制,适于大规模生产,且制得的石墨烯微球的粒径可控,粒径尺寸均一,粒径范围为50nm‑1000um。
一种石墨烯药物缓释微球及其制备方法.pdf
本发明涉及一种石墨烯药物缓释微球及其制备方法,缓释微球为药物和氧化石墨烯GO的复合微球。制备:将氧化石墨烯、药物溶于PBS溶液中,超声,室温下避光搅拌,离心,冷冻干燥,得到氧化石墨烯载药复合物;将氧化石墨烯载药复合物溶于水中,超声雾化,然后通过管式炉,并用聚四氟乙烯PTFE滤膜收集,干燥,即得。本发明制得的药物缓释微球具有pH敏感型释放的特点,可以用于抗肿瘤研究,有着很好的实用价值。
一种氮掺杂石墨烯基炭气凝胶微球的制备方法及其应用.pdf
本发明涉及凝胶微球制作及应用技术领域,具体涉及一种氮掺杂石墨烯基炭气凝胶微球的制备方法及其应用,包括如下步骤:S1将间苯二酚、甲醛、催化剂无水碳酸钠、氧化石墨烯、三聚氰胺、去离子水混合反应后,得反应溶液;S2将反应溶液加入至表面活性剂中搅拌,得均一分散的红棕色乳状液;S3将红棕色乳状液经溶胶‑凝胶反应后,再用含三氟乙酸的丙酮溶液进行老化,用丙酮浸泡后,经常压干燥得有机气凝胶;S4经碳化得石墨烯基炭气凝胶微球;S5经KOH活化得球形炭气凝胶;S5经CO
石墨烯膜球的制备方法.pdf
本发明提供一种石墨烯膜球的制备方法,包括:将氧化硅微球分散在基底表面,所述氧化硅微球在所述基底的表面为单层分布;将分散有氧化硅微球的基底放置进反应炉中;通入保护气体,排出反应炉中的空气;通入还原性气体并加热反应炉至反应温度;在保护气体及还原性气体的保护下,向反应炉通入碳源气体,经过预定反应时间,在氧化硅微球的表面直接生长石墨烯,形成石墨烯层。本发明提供的石墨烯膜球的制备方法工艺简单,且具有更长的使用寿命。
一种石墨烯制备方法及石墨烯.pdf
本发明公开一种石墨烯制备方法及石墨烯,方法包括:将鳞片石墨和盐粒按一定质量比例放置在滚筒装置内;启动滚筒装置,滚动第一混合时间,加入助剂,再滚动第二混合时间,使鳞片石墨、盐粒和助剂充分接触;将混合后的物质放入水中溶解,采用负压法过滤出固体物质,清洗固体物质,超声剥离后过滤,冻干处理,放置在3200℃高温的真空炉中升温去杂质,得到石墨烯。滚筒转动的方式保证在混合过程中只有盐粒、鳞片石墨和助剂三者之间的摩擦碰撞,使得石墨烯在不破坏物理形态的情况下,吸附在盐粒表面,保留了石墨烯完整的物理、化学性质,制备方法简单