
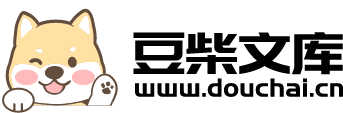
促进剂DCBS的生产工艺.pdf
猫巷****正德
在线预览结束,喜欢就下载吧,查找使用更方便
相关资料
促进剂DCBS的生产工艺.pdf
本发明属于杂环化合物领域,具体涉及一种促进剂DCBS的生产工艺,包括下述步骤:1)将MBTS与混合溶剂在搅拌条件下混合均匀,得到原料浆液;2)将混合好的原料浆液与催化剂投入氧化釜氧化;3)反应完成后即可得到目标产物DCBS。本发明采用MBTS作为主要原料,绝大程度上回避了直接氧化MBT‑二环己胺络合物的反应过程,进而大幅提高了反应的收率,且工艺比较简单,产业化转化亦比较容易。
促进剂DCBS的合成方法.pdf
本发明属于橡胶促进剂领域,具体涉及一种促进剂DCBS的合成方法,采用下述步骤:(1)将MBT、二环己胺、以及溶剂在搅拌条件下混合,待MBT全部溶解后形成原料液;(2)将配好的原料液以及双氧水,连续泵入填好催化剂的浆态床反应器中进行氧化反应(3)将浆态床反应器内流出的物料经收集后,沉降分层并收集有机相,有机相降温析出有机物;(4)过滤得到的粗DCBS经水洗,烘干后,即可得到DCBS成品。本发明的提供一种以Cu/Co/Mn三金属氧化物负载在载体上的固体催化剂为催化剂,在浆态床反应器中,制备硫化促进剂DCBS,
橡胶硫化促进剂DCBS的制备方法.pdf
本发明涉及一种橡胶硫化促进剂DCBS的制备方法,将高压反应所得的粗MBT在剧烈搅拌下直接加入到装有水的容器内,向容器内滴加氢氧化钠水溶液,使MBT全部溶解制成M-Na盐溶液,静置后将上层清液转移至计量罐;向装有异丙醇和二环己胺的容器内同时滴加次氯酸钠溶液、M-Na盐溶液、硫酸溶液,M-Na盐溶液滴加完毕后,停止滴加其余两种溶液;将反应到终点的反应混合物静置,分离出盐水及异丙醇,异丙醇直接回用,物料层进行抽滤,滤饼水洗至中性,洗料水蒸馏回收异丙醇,物料干燥得DCBS成品。该方法以MBT粗品为原料直接合成促进
一种制备橡胶促进剂DCBS的新方法.pdf
本发明公开了一种制备橡胶促进剂DCBS的新方法,属于橡胶促进剂技术领域。本发明制备橡胶促进剂DCBS的新方法,以M‑Na的醇‑水均一溶液、酸溶液、氧化剂溶液、二环己胺的醇溶液为原料,氧化合成橡胶促进剂DCBS。本发明方法所用的溶剂为乙醇溶液,二环己胺溶于乙醇。这样,在乙醇水溶液的体系中,M‑Na、硫酸、氧化剂和二环己胺能够形成均相,使反应原料更充分的接触进行反应,形成更多的目的产物,提高收率。本发明方法产品收率高,副产物少,纯度高,原料消耗低。同时在母液精馏回收乙醇后形成的废水中难处理的成分减少,减轻了后
一种橡胶硫化促进剂DCBS的合成方法.pdf
本发明涉及橡胶硫化促进剂生产技术领域,特别公开了一种橡胶硫化促进剂DCBS的合成方法。该橡胶硫化促进剂DCBS的合成方法,其特征为:往成盐釜内投入溶剂异丙醇和促进剂M后,缓慢加入二环己胺,得到M‑二环己胺盐;往氧化釜内投入溶剂异丙醇,先加入部分次氯酸钠,再同时滴加次氯酸钠和M‑二环己胺盐进行氧化反应,最终得到产品。本发明过程简单,易于实现工业化,生产中不再使用液碱和硫酸,使废水中的盐含量大大减少,节省了水处理成本,减少了原料促进剂M或二环己胺的使用量,提高了反应收率,降低了生产成本。