
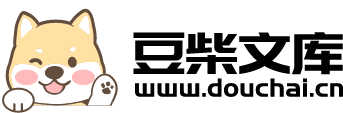
一种氧化石墨烯纳滤膜及其制备方法与应用.pdf
邻家****文章
在线预览结束,喜欢就下载吧,查找使用更方便
相关资料
一种氧化石墨烯纳滤膜及其制备方法与应用.pdf
本发明提供了一种氧化石墨烯纳滤膜及其制备方法与应用,该制备方法包括如下步骤:将含有氧化石墨烯的分散液涂布于基膜上,多胺交联后用次氯酸钠进行后处理,得到所述氧化石墨烯纳滤膜。本发明采用多胺对氧化石墨烯进行交联,提升氧化石墨烯膜的结构稳定性和性能稳定性,并进一步采用次氯酸钠进行后处理,大幅提升了纳滤膜的通量,且保持染料截留率,使其可以成功应用于废水的脱色处理。
一种混合氧化石墨烯纳滤膜、制备方法及其应用.pdf
本申请提供混合氧化石墨烯纳滤膜的制备方法,先将氧化石墨烯分散、离心,取上清液干燥定量,得到小尺寸氧化石墨烯;再将底部的沉淀物重新分散后、离心,将得到的沉淀物干燥定量,得到大尺寸氧化石墨烯;将大尺寸氧化石墨烯用纯水配置成大尺寸氧化石墨烯分散液;将小尺寸氧化石墨烯用纯水配置成小尺寸氧化石墨烯分散液;将大尺寸氧化石墨烯分散液与小尺寸氧化石墨烯分散液配置成混合氧化石墨烯分散液;混合氧化石墨烯分散液在真空条件下抽滤至聚偏氟乙烯支撑膜上,得到混合氧化石墨烯纳滤膜。制得的混合氧化石墨烯纳滤膜有效降低层间距,增长水流路径
一种氧化石墨烯复合纳滤膜及其制备方法与应用.pdf
(19)国家知识产权局(12)发明专利申请(10)申请公布号CN116020286A(43)申请公布日2023.04.28(21)申请号202310156558.8C02F1/44(2023.01)(22)申请日2023.02.23C02F9/00(2023.01)C02F1/00(2023.01)(71)申请人广东溢达纺织有限公司C02F1/66(2023.01)地址528500广东省佛山市高明区沧江出C02F101/30(2006.01)口加工区(72)发明人柯岩王姣姣谭皓坤杜希邱孝群张玉高张旋(74
一种氧化石墨烯纳滤膜及其制备方法.pdf
本申请公开了一种氧化石墨烯纳滤膜及其制备方法,所述氧化石墨烯纳滤膜包括支撑衬底层和氧化石墨烯层;所述氧化石墨烯层的厚度为120nm至200nm;所述支撑衬底层的厚度为200μm至400μm;所述支撑衬底的孔径为200nm至400nm。本申请技术方案解决了一般插层法提高氧化石墨烯纳滤膜水通量的过程中,由于两相相容性差而在膜内产生非选择性孔洞缺陷,从而引起膜截留性能恶化的问题。该方法操作简单,效果显著,与现有的氧化石墨烯膜制备工艺兼容性好,在优化膜水通量的同时可保持其截留性能不受影响,实现高效率氧化石墨烯纳滤
一种氧化石墨烯改性纳滤膜的制备方法和应用.pdf
一种氧化石墨烯改性纳滤膜的制备方法,将多孔支撑膜的一侧表面依次在水相溶液、有机相溶液、水相溶液进行界面聚合反应,然后将膜晾干、热反应后用超纯水浸泡制得氧化石墨烯改性纳滤膜。本发明仅在多孔支撑膜的一侧界面进行聚合反应,能最大限度的生成聚合物有效功能层,提高纳滤膜分离作用,同时简化制备工序,节约了成本;在水相溶液中添加了适量氧化石墨烯(GO),大大改善了纳滤膜的亲水性能、膜渗透性能以及机械性能,制得的纳滤膜的水接触角降低了18~61%,水通量提高了5~155%,截留率也有所提高;本发明工艺简单,易操作,制备的