
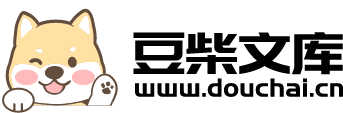
八大浪费课程.ppt
YY****。。
亲,该文档总共68页,到这已经超出免费预览范围,如果喜欢就直接下载吧~
相关资料
八大浪费课程.ppt
教材目录1.什么是浪费:(1)在制造活动中,不增加价值的所有行为,是浪费;(2)尽管是增加价值的活动,所用的资源超过了“绝对最少”的界限,也是浪费。◇实体上改变了物料的活动才能在生产过程中增加价值。◇加工零件,组装产品,油漆、包装,增值?3/223.站在客户的立场上,有四种增值的工作4.举例:下面的活动哪些才是增值的?5.浪费的三种状态不饱和vs超负荷1、三种经营思想为世界作贡献3、假效率与真效率假效率假效率4、个别效率与整体效率个别效率我们总结一下在生产中哪些属于浪费?1.2.3.4.5.6.7.8.浪
精益生产之八大浪费学习课程.pptx
课程导读第一讲:认识浪费精益生产的概念精益生产概念精益生产(准时生产)其核心是消除一切无效劳动和浪费,它把目标确定在尽善尽美上,通过不断地降低成本、提高质量、增强生产灵活性、实现无废品和零库存等手段确保企业在市场竞争中的优势。核心就是持续不断使浪费最小化流动最大化意识。精益生产精益生产思想告诉我们精益核心思想无附加价值的劳动浪费!!!超额使用资源而产生附加价值的劳动浪费!!!浪费的观念第八大浪费第二讲:八大浪费的详解浪费的层次1.制造过多的浪费1.制造过多的浪费原因:1.制造过多的浪费2.等待的浪费2.等
工厂八大浪费之管理的浪费.ppt
27九月2024一生产过剩的浪费导引目录第一部分:管理的浪费如何定义?长期以来,许多中外学者从不同的研究角度出发,对管理作出了不同的定义,然而,不同的学者在研究管理时出发点不同,因此,他们对管理一词所下的定义也就有所不同。直到目前为止,管理还没有一个统一的定义。在讨论管理定义前,我们先从管理的字面上理解:管理:是管人理事,还是管事理人?其实,道理就象我们研究“鸡”和“蛋”不一定能说明白,也不一定必须说明白管理大师对管理所下的定义法约尔:管理是所有的人类组织(不论是家庭、企业或政府)都有的一种活动,这种活动
八大浪费-.ppt
陳光權序言八大浪費介紹各種浪費的表現、浪費的原因及消除避免八大浪費的手法序言浪費的3種形態:1.勉強浪費的定義8種浪費(一)定義:生產過程中,因來料或制程不良,造成的各種損失,必需進行處置的時間﹑人力和物力的浪費.1﹑產品設計方面:設計不良、工藝設計不合理;2﹑產品生産方面:製造過程中管理影響產品品質;3﹑供應商方面:不合格的零部件產生的品質問題;4﹑不良處理方面:對已發生的不良處理不當。一﹑作業管理—標准作業指導書,標准作業,標准持有,教育訓練﹔二﹑全面品質管理(TQM)﹔三﹑品管統計手法(SQC)﹔四
工厂八大浪费.docx
精益生产与品质成本管理:工厂常见八大浪费点击:4266关键字:成本浪费品质八大管理精益生产工厂常见现场成本降低的主要手段和方法1)改进质量2)改进生产力3)降低库存4)缩短生产线5)减少机器停机时间6)减少空间7)降低生产交期品质管理不是那一个部门或那一个人的责任而是公司所有成员的共同责任需要明白的是:要从每一个小小的环节都去考虑综合起来才能做好整个产品的品质要懂得:下一工序就是客户.品质是管理出来的而不是检验出来的精益生产之品质管理强调预防不合格品的发生要从操作者机器模具工具材料和生