
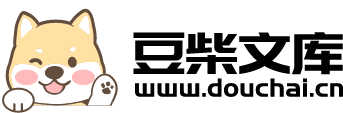
八大浪费-.ppt
lj****88
亲,该文档总共56页,到这已经超出免费预览范围,如果喜欢就直接下载吧~
相关资料
工厂八大浪费之管理的浪费.ppt
27九月2024一生产过剩的浪费导引目录第一部分:管理的浪费如何定义?长期以来,许多中外学者从不同的研究角度出发,对管理作出了不同的定义,然而,不同的学者在研究管理时出发点不同,因此,他们对管理一词所下的定义也就有所不同。直到目前为止,管理还没有一个统一的定义。在讨论管理定义前,我们先从管理的字面上理解:管理:是管人理事,还是管事理人?其实,道理就象我们研究“鸡”和“蛋”不一定能说明白,也不一定必须说明白管理大师对管理所下的定义法约尔:管理是所有的人类组织(不论是家庭、企业或政府)都有的一种活动,这种活动
八大浪费-.ppt
陳光權序言八大浪費介紹各種浪費的表現、浪費的原因及消除避免八大浪費的手法序言浪費的3種形態:1.勉強浪費的定義8種浪費(一)定義:生產過程中,因來料或制程不良,造成的各種損失,必需進行處置的時間﹑人力和物力的浪費.1﹑產品設計方面:設計不良、工藝設計不合理;2﹑產品生産方面:製造過程中管理影響產品品質;3﹑供應商方面:不合格的零部件產生的品質問題;4﹑不良處理方面:對已發生的不良處理不當。一﹑作業管理—標准作業指導書,標准作業,標准持有,教育訓練﹔二﹑全面品質管理(TQM)﹔三﹑品管統計手法(SQC)﹔四
工厂八大浪费.docx
精益生产与品质成本管理:工厂常见八大浪费点击:4266关键字:成本浪费品质八大管理精益生产工厂常见现场成本降低的主要手段和方法1)改进质量2)改进生产力3)降低库存4)缩短生产线5)减少机器停机时间6)减少空间7)降低生产交期品质管理不是那一个部门或那一个人的责任而是公司所有成员的共同责任需要明白的是:要从每一个小小的环节都去考虑综合起来才能做好整个产品的品质要懂得:下一工序就是客户.品质是管理出来的而不是检验出来的精益生产之品质管理强调预防不合格品的发生要从操作者机器模具工具材料和生
八大浪费培训.ppt
八大浪费管理培训我们的约定!为什么要讨论浪费Ⅹ销售价格=成本+利润以成本主义提高售价是无法生存的○利润=销售价格–成本降低成本增加利润思考才是根本用不同的评判
工厂八大浪费.docx
编号:时间:2021年x月x日书山有路勤为径,学海无涯苦作舟页码:第页共NUMPAGES16页第PAGE\*MERGEFORMAT16页共NUMPAGES\*MERGEFORMAT16页精益生产与品质成本管理:工厂常见八大浪费点击:4266关键字:HYPERLINK"http://www.chinavalue.net/Blog/TagEntry.aspx?TagID=1429"\t"_blank"成本HYPERLINK"http://www.chinavalue