
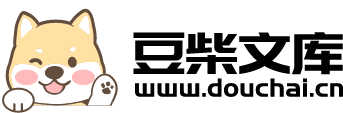
浅谈数控车床普通螺纹的加工.docx
一吃****永贺
亲,该文档总共12页,到这已经超出免费预览范围,如果喜欢就直接下载吧~
相关资料
浅谈数控车床普通螺纹的加工.doc
浅谈数控车床一般螺纹的加工在数控车床上能够车削米制、英寸制、模数和径克制四种标准螺纹,不论车削哪一种螺纹,车床主轴与刀具之间一定保持严格的运动关系:即主轴每转一转(即工件转一转),刀具应平均地挪动一个(工件的)导程的距离。以下经过对一般螺纹的剖析,增强对一般螺纹的认识,以便更好的加工一般螺纹。一、一般螺纹的尺寸剖析数控车床对一般螺纹的加工需要一系列尺寸,一般螺纹加工所需的尺寸计算剖析主要包含以下两个方面:、螺纹加工前工件直径考虑螺纹加工牙型的膨胀量,螺纹加工前工件直径D/d-0.1P,即螺纹大径减0
浅谈数控车床普通螺纹的加工.docx
编号:时间:2021年x月x日书山有路勤为径,学海无涯苦作舟页码:第页共NUMPAGES12页第PAGE\*MERGEFORMAT12页共NUMPAGES\*MERGEFORMAT12页浅谈数控车床普通螺纹的加工在数控车床上可以车削米制、英寸制、模数和径节制四种标准螺纹,无论车削哪一种螺纹,车床主轴与刀具之间必须保持严格的运动关系:即主轴每转一转(即工件转一转),刀具应均匀地移动一个(工件的)导程的距离。以下通过对普通螺纹的分析,加强对普通螺纹的了解,以便更好的加工普通螺纹。一、普通螺纹
浅谈数控车床普通螺纹的加工.docx
编号:时间:2021年x月x日书山有路勤为径学海无涯苦作舟页码:浅谈数控车床普通螺纹的加工在数控车床上可以车削米制、英寸制、模数和径节制四种标准螺纹无论车削哪一种螺纹车床主轴与刀具之间必须保持严格的运动关系:即主轴每转一转(即工件转一转)刀具应均匀地移动一个(工件的)导程的距离。以下通过对普通螺纹的分析加强对普通螺纹的了解以便更好的加工普通螺纹。一、普通螺纹的尺寸分析数控车床对普通螺纹的加工需要一系列尺寸普通螺纹加工所需的尺寸计算分析
数控车床普通螺纹的加工.docx
数控车床普通螺纹的加工数控车床普通螺纹的加工【1】摘要:在日常生活中,随处都可以见到螺丝钉或是螺丝帽相关的东西,可以说人们的日常生活用品离不开这些东西,它与人们的生活息息相关。无论是螺丝钉,还是螺丝帽或一些其他的与螺丝相关的东西都是由螺纹构成的。在机械工业制造中,这些带有螺纹的零件运用的相当的广泛,而螺纹的加工却是一个难点。因此,想要快速高效的提升产品的价值,必须要提高螺纹的质量。关键词:螺纹的对刀;螺纹的加工;螺纹的检测在起亚数控车床上可以车削的螺纹包含了四种标准,分别是米制、英寸制、模数与径节制。无论
数控车床普通螺纹的加工.docx
数控车床普通螺纹的加工数控车床普通螺纹的加工数控车床普通螺纹的加工【1】摘要:在日常生活中,随处都可以见到螺丝钉或是螺丝帽相关的东西,可以说人们的日常生活用品离不开这些东西,它与人们的生活息息相关。无论是螺丝钉,还是螺丝帽或一些其他的与螺丝相关的东西都是由螺纹构成的。在机械工业制造中,这些带有螺纹的零件运用的相当的广泛,而螺纹的加工却是一个难点。因此,想要快速高效的提升产品的价值,必须要提高螺纹的质量。关键词:螺纹的对刀;螺纹的加工;螺纹的检测在起亚数控车床上可以车削的螺纹包含了四种标准,分别是米制、英寸