
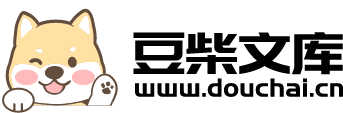
生产环境下的八大浪费培训课件.pptx
hj****27
亲,该文档总共49页,到这已经超出免费预览范围,如果喜欢就直接下载吧~
相关资料
生产环境下的八大浪费培训课件.pptx
2024/11/7现场互动:目的内容目录组织经营活动顾客只愿意为那5%的增值掏腰包!浪费的定义——不为产品增加价值的任何事情——不利于生产、不符合客户要求的任何事情——顾客不愿付钱由你去做的任何事情——尽管是增加价值的活动,但所用的资源超过了“绝对最少”的界限,也是浪费不良品定义:由于原材料本身是不良品或制造过程中产生的不良品、设计缺陷等造成的各种损失。来料不良供应商来料本身不良;运输过程中损坏;进料检验、本工序投料检查或后工序未发现等供应商审查、辅导定义:前工序的投入量,超过后工序单位时间内的需求量,而
生产环境下的八大浪费培训课件.pptx
2024/11/22现场互动:目的内容目录组织经营活动顾客只愿意为那5%的增值掏腰包!浪费的定义——不为产品增加价值的任何事情——不利于生产、不符合客户要求的任何事情——顾客不愿付钱由你去做的任何事情——尽管是增加价值的活动,但所用的资源超过了“绝对最少”的界限,也是浪费不良品定义:由于原材料本身是不良品或制造过程中产生的不良品、设计缺陷等造成的各种损失。来料不良供应商来料本身不良;运输过程中损坏;进料检验、本工序投料检查或后工序未发现等供应商审查、辅导定义:前工序的投入量,超过后工序单位时间内的需求量,
生产环境下的八大浪费-经典教程.ppt
2024/10/23现场互动:目的内容目录组织经营活动顾客只愿意为那5%的增值掏腰包!浪费的定义——不为产品增加价值的任何事情——不利于生产、不符合客户要求的任何事情——顾客不愿付钱由你去做的任何事情——尽管是增加价值的活动,但所用的资源超过了“绝对最少”的界限,也是浪费不良品定义:由于原材料本身是不良品或制造过程中产生的不良品、设计缺陷等造成的各种损失。来料不良供应商来料本身不良;运输过程中损坏;进料检验、本工序投料检查或后工序未发现等供应商审查、辅导定义:前工序的投入量,超过后工序单位时间内的需求量,
生产环境下的八大浪费-经典教程.pptx
2024/11/21现场互动:目的内容目录组织经营活动顾客只愿意为那5%的增值掏腰包!浪费的定义——不为产品增加价值的任何事情——不利于生产、不符合客户要求的任何事情——顾客不愿付钱由你去做的任何事情——尽管是增加价值的活动,但所用的资源超过了“绝对最少”的界限,也是浪费不良品定义:由于原材料本身是不良品或制造过程中产生的不良品、设计缺陷等造成的各种损失。来料不良供应商来料本身不良;运输过程中损坏;进料检验、本工序投料检查或后工序未发现等供应商审查、辅导定义:前工序的投入量,超过后工序单位时间内的需求量,
八大浪费培训ppt课件.ppt
1/222/22▶4/22二、浪费使企业走向衰亡6/2218/229/22计划有误维修问题效率问题能力不平衡质量问题交货问题2)库存降低会暴露问题搬运并不直接产生价值,也不对产品附加值作出贡献约85%搬运浪费搬运浪费其它2约25%-40%是搬运费工厂灾害有些人利用传送带的方式来减少“搬运”,此谓治标不治本,造成搬运的流程问题并没解决。生产流水化同步化是减少搬运的根本之道带来的问题材料的损失设备、人员工时的损失额外的修复、挑选、追加检查额外的检查预防人员降价处理出货延误取消定单信誉下降不良、返工、召回造成企