
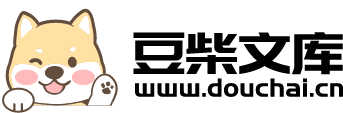
八大浪费培训ppt课件.ppt
lj****88
亲,该文档总共32页,到这已经超出免费预览范围,如果喜欢就直接下载吧~
相关资料
八大浪费培训ppt课件.ppt
1/222/22▶4/22二、浪费使企业走向衰亡6/2218/229/22计划有误维修问题效率问题能力不平衡质量问题交货问题2)库存降低会暴露问题搬运并不直接产生价值,也不对产品附加值作出贡献约85%搬运浪费搬运浪费其它2约25%-40%是搬运费工厂灾害有些人利用传送带的方式来减少“搬运”,此谓治标不治本,造成搬运的流程问题并没解决。生产流水化同步化是减少搬运的根本之道带来的问题材料的损失设备、人员工时的损失额外的修复、挑选、追加检查额外的检查预防人员降价处理出货延误取消定单信誉下降不良、返工、召回造成企
工厂八大浪费之管理的浪费培训资料ppt课件.ppt
一生产过剩的浪费导引目录第一部分:管理的浪费如何定义?长期以来,许多中外学者从不同的研究角度出发,对管理作出了不同的定义,然而,不同的学者在研究管理时出发点不同,因此,他们对管理一词所下的定义也就有所不同。直到目前为止,管理还没有一个统一的定义。在讨论管理定义前,我们先从管理的字面上理解:管理:是管人理事,还是管事理人?其实,道理就象我们研究“鸡”和“蛋”不一定能说明白,也不一定必须说明白管理大师对管理所下的定义法约尔:管理是所有的人类组织(不论是家庭、企业或政府)都有的一种活动,这种活动由五项要素组成:
工厂常见八大浪费ppt课件.ppt
工厂中常见的八大浪费和改善方法浪费的定义各种各样的浪费现象在很多尚未实行5S活动的企业中普遍存在,如表1-1所示。为了杜绝工厂中的浪费现象,首先需要发现不合理的地方,然后才是想办法解决问题,这就需要推行5S、JIT等较为先进的管理方法。浪费表现工厂常见八大浪费工厂常见八大浪费工厂常见八大浪费工厂常见八大浪费工厂常见八大浪费工厂常见八大浪费工厂常见八大浪费工厂常见八大浪费工厂常见八大浪费工厂常见八大浪费工厂常见八大浪费工厂常见八大浪费工厂常见八大浪费工厂常见八大浪费工厂常见八大浪费工厂常见八大浪费
八大浪费及八大改善教材ppt课件.ppt
八大浪费八大改善步骤一、浪费定义?二、工厂常见的八大浪费三、IE改善常用工具四、八大改善步骤1.什么是浪费:(1)在制造活动中,不增加价值的所有行为,是浪费;(2)尽管是增加价值的活动,所用的资源超过了“绝对最少”的界限,也是浪费。◇实体上改变了物料的活动才能在生产过程中增加价值。◇加工零件,组装产品,油漆、包装,增值?浪不良造成额外成本源头=$1生产过程=$10发货=$100顾客=$1,000原因:1.5我们的现状??浪过分精确或超标准过多的确认和批准额外的复制/过多的信息与另外工序可以合并的工作2.3
生产环境下的八大浪费培训课件.pptx
2024/11/7现场互动:目的内容目录组织经营活动顾客只愿意为那5%的增值掏腰包!浪费的定义——不为产品增加价值的任何事情——不利于生产、不符合客户要求的任何事情——顾客不愿付钱由你去做的任何事情——尽管是增加价值的活动,但所用的资源超过了“绝对最少”的界限,也是浪费不良品定义:由于原材料本身是不良品或制造过程中产生的不良品、设计缺陷等造成的各种损失。来料不良供应商来料本身不良;运输过程中损坏;进料检验、本工序投料检查或后工序未发现等供应商审查、辅导定义:前工序的投入量,超过后工序单位时间内的需求量,而