
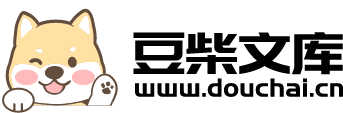
焊接轨道式起重机主梁.pdf
邻家****曼玉
在线预览结束,喜欢就下载吧,查找使用更方便
相关资料
焊接轨道式起重机主梁.pdf
焊接轨道式起重机主梁。它是将起重机小车运行轨道与箱形主梁的上翼缘板或桁架式主梁的上弦杆焊接,使箱形主梁的加劲肋间距由0.5m增大到0.75m,从而减小起重机箱形主梁上翼缘板和加劲肋用钢量,减小桁架式主梁上弦杆用钢量;由于轨道与起重机主梁焊接,节省了轨道压板并避免轨道松动,从而减小起重机轨道维护保养工作量。
新型起重机主梁滑车.pdf
本发明公开了一种新型起重机主梁滑车,包括由两块承重提升板组成的车体,所述车体上端两侧设有若干车轮,车体上端前后两侧设有二次防护板,车体的下端为一车架,所述车架中间呈中空状,所述车架的下端连接一电缆支撑架,所述电缆支撑架呈开口向下的圆弧状,所述电缆支撑架的中间设有一用于调节电缆支撑架与车架之间距离的调节螺母,所述调节螺母的上端与车架上的螺孔连接,本发明的车轮能够与专门配套使用的轨道实现自动校正路线,降低摩擦系数等自动功能,其各部件严格通过特殊工艺加工而成,最后通过各部件的组装,即可实现与吊钩或带有吊耳的提升
铸造起重机主梁局部焊接结构疲劳性能研究的任务书.docx
铸造起重机主梁局部焊接结构疲劳性能研究的任务书任务书一、研究背景与意义铸造起重机主梁是现代起重运输设备中的重要组成部分,它承担着大量重物的起吊和运输任务。通过对主梁局部焊接结构疲劳性能研究,可以有效提高铸造起重机的安全性能和使用寿命,降低设备维修及更换成本,提高设备的生产率和经济效益。二、研究内容1.研究对象:本次研究的对象为铸造起重机主梁局部焊接结构。2.研究方法:采用推导数学模型、有限元模拟、实物试验等方法,分析局部焊接结构的疲劳性能,并建立疲劳寿命预测模型。3.研究内容:(1)对主梁局部焊接结构进行
门式起重机主梁制造工艺研究-陆锦枝.doc
门式起重机主梁焊接工艺研究新上铁上海修造分公司陆锦枝摘要:上海修造分公司今年承接了多台门式起重机的制造任务后,通过对主梁主材Q235B钢的材料化学分析、焊接要求分析后,初步确定焊接方法和焊接材料,制定了焊接工艺评定方案,按焊接工艺评定要求进行力学试验,根据试验结果制定了详细的焊接加工工艺并制作样品进行承载试验,试验结果证明焊接工艺可行。关键词:门式起重机主梁焊接工艺研究一、问题的提出今年新上铁修造分公司承接多台门式起重机的制造任务,按照门式起重机的设计要求,一般门式起重机的主梁使用的主要材料为Q235B,
起重机主梁制造改造的方法.pdf
一种起重机主梁制造改造的方法,通过在主梁跨中梁与支撑架之间焊接工字钢支架及加固筯,并在主梁中部下端用螺栓安装张拉器,在支撑架顶端与主梁悬臂末端通过连接座安装张拉器,并采用张拉系统对张拉器进行张拉,使主梁跨中梁的上拱度满足标准要求,主梁悬臂满足有效悬臂处的上翘度为0.9/350‑1.4/35。本发明起重机主梁制造改造的方法,易加工制造、成本低、施工方便,适用于任何吨位的起重机主梁制造或改造,尤其适用于港口、造船行业的门式起重机制造改造。经制造或改造的起重机两主梁上拱差保持在0‑1毫米范围内,起重机主梁始终保