
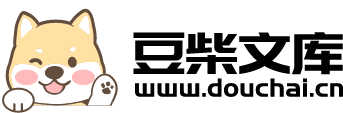
脱硫石膏制粉的优化工艺.pdf
as****16
在线预览结束,喜欢就下载吧,查找使用更方便
相关资料
脱硫石膏制粉的优化工艺.pdf
脱硫石膏制粉的优化工艺含金沙摘要:近年来,随着我国工业的发展,电厂脱硫石膏越来越多,如何将脱硫石膏工业化利用,才是我们迫切要解决的问题。本文就脱硫石膏制取β建筑石膏和α石膏的工艺进行优化组合。关键词:脱硫石膏;工艺技术;α石膏;转晶剂1前言电厂烟气脱硫石膏(FDG)呈细粉状,其中二水硫酸钙含量可高达95%,是一种很好的石膏资源,可与天然石膏等效。在国外特别是欧洲,几乎所有的脱硫石膏都被回收利用。主要用于β建筑石膏粉、α石膏粉、水泥缓凝剂、石膏制品、石膏砂浆等石膏建材产品。国内对于脱硫石膏的综合利用处理和应
脱硫石膏制备高强石膏工艺现状.docx
脱硫石膏制备高强石膏工艺现状脱硫石膏制备高强石膏工艺现状摘要:石膏作为空气污染物产生的主要固体废弃物之一,其高效利用对环境治理和资源可持续利用具有重要意义。本文综述了脱硫石膏制备高强石膏的工艺现状,包括湿法和干法两种主要工艺路线,并介绍了其中的关键技术。通过对不同工艺的比较分析,得出了相对于传统工艺路线,干法工艺具有更低的能耗和更高的石膏产量的优势,并提出了干法工艺的进一步改进方向,以实现更高的强度和可塑性目标。此外,还讨论了脱硫石膏高强石膏在建筑材料领域的应用前景。关键词:脱硫石膏;高强石膏;工艺现状;
脱硫石膏制备低氯建筑石膏的工艺.pdf
脱硫石膏制备低氯建筑石膏的工艺,该工艺流程为:将电厂排出的脱硫石膏先送入清洗机中进行清洗,通过真空过滤、喷淋水洗、抽干,备用;将清洗后的脱硫石膏原料进行破碎,并送入干燥机内进行初步烘干,干燥温度为80~160℃;烘干后的脱硫石膏输送至煅烧炉进行煅烧,煅烧温度为120~230℃;煅烧后的物料通过冷却出料输送机构进行降温及输送,冷却后由提升机提升至改性磨进行粉磨,然后进入均化库进行均化;本发明可有效处理火电厂固废脱硫石膏,不仅能避免因堆放而引起的二次污染问题,还能变废为宝,促进我国燃煤电厂烟气、钢铁烧结机烟气
脱硫石膏在建筑石膏上的应用工艺.doc
脱硫石膏(FGD)在建筑石膏上的应用工艺贾兴福长沙巨星轻质建材股份有限公司湖南长沙(410000)摘要在2010年之后,我国每年将要排放近亿吨燃煤电厂烟气脱硫的副产品——脱硫石膏;同时每年还要排放与脱硫石膏同属化学石膏的磷石膏4000多万吨;2007年我国天然石膏的产量为5000多万吨,这样即使全部化学石膏全部取代了天然石膏,仍可能有几千万吨的脱硫石膏和磷石膏无法利用。由此可见,如果不对化学石膏的处理技术加以创新、开拓新的用途,进行全面的综合利用,必定会造成二次污染。在发展循环经济、节能减排的政策推动下,
一种脱硫石膏制备建筑石膏的工艺方法.pdf
本发明提出了一种脱硫石膏制备建筑石膏的工艺方法,针对脱硫石膏采用预烘干和煅烧炉煅烧的两段生产工艺进行生产,确定了脱硫石膏煅烧工艺的最优参数;本发明根据脱硫石膏的综合利用问题,提出一种低成本、高品质的煅烧工艺、并对煅烧后的脱硫建筑石膏及其在墙体材料中的应用进行研究,推进脱硫石膏的广泛应用。