
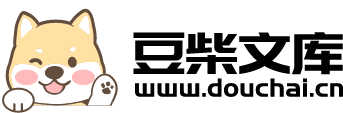
第11讲 冷连轧艺过程的板形控制技术.doc
kp****93
亲,该文档总共12页,到这已经超出免费预览范围,如果喜欢就直接下载吧~
相关资料
第11讲 冷连轧艺过程的板形控制技术.doc
轧材质量控制与深加工技术第十讲冷连轧工艺过程的板形控制技术1轧机板形概念板带材冷轧机的发展,其基本设计思想是如何提高冷轧板带的产量和质量、减少建设成本和维护费用。板带材产品有四大质量指标:板形精度、厚度精度、表面质量、力学性能。厚度精度是指板带材的平均厚度。由于现代液压、检测和控制技术的发展,自动厚度控制AGC(AutomaticGaugeControl)的引入,使得厚度控制精度大大提高,至90年代末发展已经比较成熟。表面质量是指带钢表面的缺陷情况和涂镀质量。力学性能是指带钢的强度和延展性。板形的概念并不
冷连轧升降速过程板形变化及其张力补偿技术.pptx
汇报人:目录PARTONEPARTTWO冷连轧工艺的基本原理冷连轧工艺的特点冷连轧工艺的应用范围PARTTHREE升降速过程中板形变化的原理升降速过程中板形变化的影响因素升降速过程中板形变化的控制方法PARTFOUR张力补偿技术的原理张力补偿技术在冷连轧中的重要性张力补偿技术的实现方式PARTFIVE基于工艺参数的优化策略基于设备结构的优化策略基于控制算法的优化策略PARTSIX智能化张力补偿技术的发展趋势基于大数据和云计算的张力补偿技术应用前景绿色环保的张力补偿技术发展方向THANKYOU
过程控制工程-冷连轧张力控制.ppt
过程控制工程——冷连轧张力控制2轧制过程中张力的产生原因张力的产生:由于在轧件长度方向上存在着速度差,使得轧件上不同部位处的金属有相对位移而产生张应力⇒张力张力大小的表示:以平均单位张力(张应力)σTm乘以所作用的横截面积A就是作用在轧件上的张力T,张力是由于机架间速度不协调而造成的,从两个机架来看,如果由于某种原因(外扰量或调节量变动时)而使第i机架带钢出口速度减小(可以是轧辊速度减小,也可能是由于压下量等其他工艺参数变动,造成前滑量减小)或使第i+1机架带钢入口速度加大,结果使第i和i+1机架间的带钢
带钢非稳态冷连轧过程厚度与张力控制.docx
带钢非稳态冷连轧过程厚度与张力控制导言:随着工业技术的不断发展,带钢制造业也在不断地进行革新和变革。带钢的制造过程和技术是重要的研究方向之一。其中,带钢非稳态冷连轧过程厚度与张力控制是一个重要的研究方向,不仅关系到带钢的品质和规格,还能提高带钢的生产效率和降低制造成本。因此,对带钢非稳态冷连轧过程厚度与张力控制进行深入研究具有重要的实际意义和理论价值。正文:一、非稳态冷连轧过程(1)带钢制造流程带钢是将钢板经过连续冷轧和切割成所需的规格尺寸。带钢的制造过程通常分为钢坯准备、粗轧、中轧、精轧和切割几个过程。
浅谈热连轧板形控制及影响因素.doc
浅谈热连轧板形控制及影响因素姓名:刘明单位:热轧板厂轧钢车间浅谈热连轧板形控制及影响因素【摘要】本文针对热轧板形的控制.简要分析了影响板形的主要因素的方法.简要提出工艺和设备控制的方法。【关键词】板形,.影响因素,控制方法【前言】板形是板带材质量的重要指标之一,随着市场经济的日益激烈,用户对板形的质量的要求越来越高.在生产过程中,经常出现单边浪,双边浪,楔形,凸度超标~~等等板形缺陷。如何得到良好的板形的,影响板形的因素有那些..如何控制板形,自我总结出了以下几点。一.板形的概念板形是横截面形状(Prof