
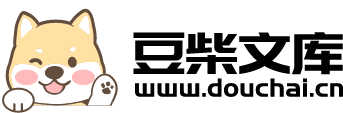
一种高强度和超高强度钢板的加工方法.pdf
冷霜****魔王
在线预览结束,喜欢就下载吧,查找使用更方便
相关资料
一种高强度和超高强度钢板的加工方法.pdf
一种高强度和超高强度钢板的加工方法为,按C:0.05~0.5%、Si:0.1~1.8%、Mn:0.1~1.9%、适宜的微量合金元素及余下为Fe的化学成份冶炼好钢坯,加热轧制成钢板,高强度钢板也可采用普通钢板,通过牵引装置送入预热中频和超音频加热炉分段加热、扁方筒形淬火装置快速淬火、回火中频加热炉回火、冷却装置冷却加工而成,其屈服强度≥600~1670MPa,比普通钢板高1~6倍,回火金相组织为屈氏体或索氏体,晶粒度达到9级以上,具有良好的抗低温冲击性,性价比优越,可广泛用于高层建筑、大跨度钢结构、船舶制造
超高强度钢板的制造方法及超高强度钢板.pdf
本发明涉及一种生产超高强度热轧结构钢的方法,其中所生产的钢具有不大于0.2%的碳含量,其中为了避免奥氏体的扩散相变,通过添加锰、铬和硼获得足够的相变延迟,其中以已知方式铸造钢材,并且铸造材料经历为了热轧目的的温度升高,其中紧接着轧制工序之后直接硬化带材,其中马氏体组织由变形的奥氏体形成,然后将以此方式生产的材料进行机械矫直,以产生可移动位错,然后对材料进行退火,以调节所需的弹性极限强度或屈服强度,同时保留直接硬化后存在的拉伸强度、韧性和成形性能,其中退火温度在100到200℃之间。
一种高强度和超高强度钢管的加工方法.pdf
一种高强度和超高强度钢管其加工方法为,按C:0.05~0.5%、Si:0.1~1.8%、Mn:0.1~1.9%、选择以下一种或几种微量合金元素:Cr:0.1~0.6%、Ni:0.1~0.5%、Nb:0.02~0.5%、Ti:0.02~0.6%、V:0.01~0.1%及余下为Fe的化学成份冶炼好钢坯,加热轧制成钢管,高强度钢管也可采用普通无缝钢管和焊管,通过牵引送入中频和超音频加热炉分段加热、筒形淬火装置快速淬火、回火中频加热炉回火、冷却装置冷却至常温加工而成,其屈服强度≥600~1670MPa,比普通钢管
一种高强度和超高强度型钢的加工方法.pdf
一种高强度和超高强度型钢其加工方法为按C:0.11~0.5%、Si:0.1~1.9%、Mn:0.1~1.9%、适宜的微量合金元素及余下为Fe的化学成份冶炼好钢坯,加热轧制成型钢,高强度型钢也可采用现有普通型钢,通过牵引送入中频和超音频加热炉加热、筒形淬火装置快速淬火、回火中频加热炉回火、冷却装置冷却加工而成,其屈服强度≥600~1670MPa,比普通型钢高1~6倍,回火金相组织为屈氏体或索氏体,晶粒度达到9级以上,具有良好的抗低温冲击性,性价比优越,可广泛用于高层建筑、大跨度钢结构、支承铁塔等重大项目工程
弯曲加工性优异的超高强度钢板及其制造方法.pdf
本发明涉及一种用作车辆的材料的超高强度钢板,更具体地,涉及一种弯曲加工性优异的超高强度钢板及其制造方法。根据本发明,使用不具有水冷(waterquenching)设备的连续退火炉,从而相比现有的超高强度马氏体钢,可以提供确保1200MPa以上的拉伸强度的同时具有优异的形状和弯曲特性的钢板。