
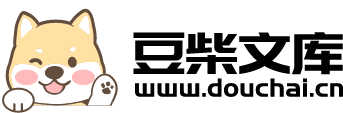
一种带钢表面火焰清洗方法及装置.pdf
哲妍****彩妍
在线预览结束,喜欢就下载吧,查找使用更方便
相关资料
一种带钢表面火焰清洗方法及装置.pdf
一种带钢表面火焰清洗方法及装置,带钢进入带钢热处理炉,带钢热处理炉包括入口密封、烟气预热段、直火清洗预热段、出口密封和加热段;带钢经入口密封进入烟气预热段,在烟气预热段经自直火清洗预热段过来的烟气逆流换热,然后进入直火清洗预热段,直火清洗预热段内布置有烧嘴,烧嘴喷出高温冲击火焰,带钢在高温冲击火焰的燃烧与冲击作用下,将带钢温度加热到300-400℃,实现均匀加热并清洗带钢表面的残油与残铁,最后经出口密封进入加热段;烧嘴喷口为狭缝型,形成均匀的条形火焰,垂直于带钢表面,构成带钢单面或者双面加热。本发明通过控
冷轧带钢的表面清洗装置.pdf
本发明公开的属于冷轧带钢清洗技术领域,具体为冷轧带钢的表面清洗装置,包括操作台和传输机构,所述传输机构置于操作台上,所述传输机构从左向右传输,所述操作台的上表面左右两侧分别设置有除尘罩和清洗罩,所述除尘罩和清洗罩的左右端均呈中空状,所述除尘罩的上表面左侧连接有压杆,所述压杆延伸至除尘罩的内部,通过除尘罩、清洗罩及其上的设备集成在操作台上,在使用时,不需要二次调试,操作较为方便;首先对冷轧带钢表面浮沉清除并使得未被清除的残留灰尘被刮起,从而方便后续清洗作用;通过喷头能够进行喷水清洗作用,通过刮板、毛刷体能够
一种带钢清洗装置.pdf
本发明公开了一种带钢酸洗装置,包括放卷机、酸洗槽、收卷机、以及热水循环系统,该热水循环系统包括热水箱和第一水泵,第一水泵的出口端依次连接有两个热水炉和第二水泵,第二水泵的出口管道连接有第一支管和第二支管;第一支管连接有至少一个第一换热器,第一换热器的出口管道连接至热水炉的进水管,第二支管连接有至少一个第二换热器,第二换热器的出口管道连接至热水炉的进水管;酸洗槽的出口管道连接一台酸泵,酸泵的出口端连接循环管,该循环管连接第一换热器和第二换热器后连接至酸洗槽的进口管道。本发明提供的带钢酸洗装置采用两个热水炉串
一种涂镀机组带钢表面的清洗方法.pdf
本发明涉及一种涂镀机组带钢表面的清洗方法,其技术方案是:先对带钢表面进行碱液喷洗,再对碱液喷洗后的带钢表面进行碱液刷洗,碱液喷洗和碱液刷洗用的碱液分别为各自清洁碱液罐中5~6%的碱液;然后分别采用高压喷淋热水罐、刷洗热水罐和喷淋热水罐的热水对碱洗后的带钢表面依次进行高压水喷淋、热水刷洗和热水喷淋,最后送至退火炉烘干。碱液喷洗后和碱液刷洗后的碱液轮换进入离心机进行渣液分离,分离后的碱液送至对应第一清洁碱液罐和第二清洁碱液罐;分离后的残渣送入残渣成型装置挤压成块。本发明具有工艺简单、成本低、能有效清除碱液中的
带钢漂洗装置、带钢酸洗系统及酸洗带钢清洗方法.pdf
本发明涉及一种带钢漂洗装置,其上漂洗机构包括第一喷嘴组和第二喷嘴组,各第一喷嘴朝向来料侧斜向下喷射并且其射流与带钢运行通道之间的相交轨迹为直线,各第二喷嘴的射流与带钢运行通道之间的相交轨迹为实心圆,实心圆轨迹位于直线轨迹的下游;和/或,其下漂洗机构包括至少一组第三喷嘴组,各第三喷嘴的射流与带钢运行通道之间的相交轨迹为实心圆。另外还涉及采用该带钢漂洗装置的带钢酸洗系统和酸洗带钢清洗方法。本发明中,第一喷嘴组可对带钢上表面的残留酸液进行清理,第二喷嘴组能在带钢上表面形成液膜层,第三喷嘴组能在带钢下表面形成液幕