
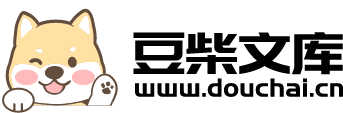
一种含铬高硅钢薄带及其制备方法.pdf
慧红****ad
在线预览结束,喜欢就下载吧,查找使用更方便
相关资料
一种含铬高硅钢薄带及其制备方法.pdf
本发明涉及一种含铬高硅钢薄带及其制备方法。其技术方案是:高硅钢薄带的硅含量为5.5~7.0wt%,铬含量为0.05~10.0wt%,其余为铁及不可避免的杂质。制备方法是:先按所述含铬高硅钢薄带的化学组分,以工业纯铁、商业用硅和纯铬为原料配料;再采用中频真空感应炉熔炼原料,在1250℃~1650℃条件下浇铸成铸坯,将铸坯在800℃~1250℃条件下锻造成厚度为10~20mm的板坯,然后将板坯在700℃~1250℃条件下热轧成厚度为0.6~0.8mm的薄带,最后将薄带在150℃~750℃条件下温轧至0.2~0
一种取向高硅钢薄带及其制备方法.pdf
本发明涉及一种取向高硅钢薄带及其制备方法。其技术方案是:取向高硅钢薄带的化学成分是:Si为5.5~6.8wt%;Cu为0.3~0.6wt%;Al为0.1~0.3wt%;S为0.01~0.015wt%;N为0.005~0.01wt%;其余为Fe和不可避免的杂质。按取向高硅钢薄带的化学成分冶炼,在1300~1650℃浇铸成板坯,将板坯在1000~1200℃热轧成厚度为0.8~1.5mm的热轧板。将热轧板常化处理,在150~450℃温轧至0.3~0.6mm,在室温条件下冷轧至0.1~0.3mm,在700~120
一种高硅硅钢薄带的制备方法.pdf
本发明提供一种高硅硅钢薄带的制备方法,将粒度<150μm纯铁粉末与粒度<74μm的硅铁粉或硅铁合金粉混合成含Si6wt%~6.5wt%的高硅铁粉,向高硅铁粉中加入润滑剂并在混料机中混合;利用二辊轧机轧制得到粉末生带;将粉末生带置于气氛炉中加热预烧结后,再利用二辊轧机进行轧制;轧后再用气氛炉进行烧结致密化;其后用二辊轧机冷轧出厚度0.2~0.3mm、宽度100~200mm的高硅硅钢薄带;利用气氛炉对高硅硅钢薄带分别进行退火处理和精整,制得6.5%Si的成品高硅硅钢薄带。本发明操作工艺简单,能够实现多尺寸、
一种基于合金化的高硅钢薄带及其制备方法.pdf
本发明涉及一种基于合金化的高硅钢薄带及其制备方法。其技术方案是:高硅钢薄带的硅含量为5.5~7.0wt%,铜含量为0.05~2.5wt%,其余为铁及不可避免的杂质。制备方法是:先按所述高硅钢薄带的化学组分,以工业纯铁、商业用硅和纯铜为原料配料;再采用中频真空感应炉熔炼原料,在1300℃~1650℃条件下浇铸成铸坯;将铸坯在750℃~1250℃条件下锻造成厚度为10~20mm的板坯;然后将板坯在700℃~1250℃条件下热轧成厚度为0.6~0.8mm的薄带;最后将薄带在150℃~750℃条件下温轧至0.2~
一种无取向硅钢薄带及其制备方法.pdf
本发明属于冶金技术与材料科学领域,具体涉及一种无取向硅钢薄带及其制备方法。本发明所涉及的无取向硅钢薄带,其化学成分按重量百分比计为:Si:3.0~3.6%,Al:0.6~1.0%,Mn:0.1~0.6%,N≤0.005%,S≤0.004%,P≤0.02%,O≤0.003%,C≤0.005%,余量为Fe。无取向硅钢在真空冶炼炉中进行冶炼;然后进行双辊薄带铸轧;铸带在1100℃~1150℃常化3min~5min;预热150℃~300℃进行冷轧;最后进行再结晶退火。该制备方法工艺简单,能耗低,成材率高,产品磁性