
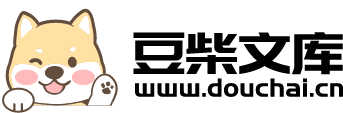
一种强化转炉钒渣钙化提钒的方法.pdf
是你****嘉嘉
在线预览结束,喜欢就下载吧,查找使用更方便
相关资料
一种强化转炉钒渣钙化提钒的方法.pdf
本发明公开了一种强化转炉钒渣钙化提钒的方法,包括以下步骤:工业选铁后的含钒渣作为原料进行破碎,然后磁选得到钒渣细粉;再将所述钒渣细粉进行球磨活化得到活化钒渣;然后将活化钒渣配加粉末状含钙化合物粉混匀得到配钙混料;然后将配钙混料在氧化焙烧炉中氧化焙烧,再空冷并破碎,得到焙烧熟料;将焙烧熟料在弱酸溶液中浸出得到含钒浸出液,所述含钒浸出液用于后续净化提钒。本方法能够降低转炉钒渣氧化焙烧温度,提高焙烧熟料中钒的浸出率。
一种钙化提钒尾渣回收钒的方法.pdf
本发明公开了一种钙化提钒尾渣回收钒的方法,属于冶金技术领域。所述方法包括以下步骤:步骤一:对钙化提钒尾渣进行打浆;步骤二:向步骤一制得的浆料中加入氧化钙,调节pH值到10~13,反应5~15min;步骤三:向步骤二的体系中加入硫酸,调节pH值到0.5~2.5,进行二次浸出,反应10~30min后固液分离,得到含钒溶液和低钒含量的二次浸出尾渣。本发明采用钙化焙烧—硫酸浸出工艺所产生的尾渣为原料,利用氧化钙使尾渣中不能被酸溶解的五氧化二钒以及水解沉钒产生的不能溶解于酸的多钒酸盐转化成溶于酸的钒酸钙,之后可以用
一种转炉钒渣冷却提钒的方法.pdf
本发明涉及一种转炉钒渣冷却提钒的方法,属于氧化钒的提取领域。本发明的技术方案为,转炉钒渣的预处理方法为:步骤A,向渣罐中盛装熔融状转炉钒渣并利用余热保温18h~24h,再使渣罐内的热钒渣分散、暴露在大气中急速冷却到常温,得到冷却钒渣;步骤B,磁选、破碎和磨细步骤A得到的冷却钒渣,得到粒度≤0.125mm、磁性物含量≤2.5%的精钒渣。本发明通过控制转炉钒渣冷却温度与时间,使钒尖晶石颗粒充分长大,加快焙烧过程中低价钒的氧化速度,提高氧化钒提取的钒收率。
热态钒渣直接钙化提钒的方法.pdf
本发明属于钒的冶金技术领域,具体涉及热态钒渣直接钙化提钒的方法。本发明所要解决的技术问题是提供一种钒回收率高、吨钒成本低的热态钒渣直接钙化提钒的方法。该方法包括如下步骤:a、将转炉提钒的热态钒渣加入冶炼炉内,以氧气或空气中的至少一种为载体通过喷吹的方式将钙质添加剂加入至热态钒渣中,得到含钙热态钒渣;b、对含钙热态钒渣进行顶吹氧化,得到钒渣熟料;c、将钒渣熟料破碎,研磨后浸出,除杂,沉淀,煅烧得V
从转炉钒渣提钒后的尾渣中再次提钒的方法.pdf
从转炉钒渣提钒后的尾渣中再次提钒的方法,该方法包括用提钒后的转炉钒渣的尾渣、浸取剂硫酸和氧化剂硫酸亚铁混合,以制备矿浆液;将所得矿浆液置于无隔膜浸取槽中,以进行电催化氧化反应;对经电催化氧化反应后的矿浆液进行固液分离,得含硫酸氧钒的滤液等步骤。在得到含硫酸氧钒的滤液后,再通过常规的现有技术,或制备出硫酸氧钒或其水合物;也可制备出五氧化二钒,或进一步还原出钒。本发明能够更多地提取现有技术基本不能再所述尾渣中进一步提出的钒,是成本较低、资源化利用较好的方法。