
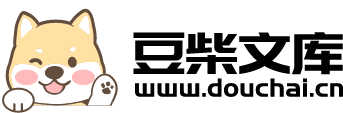
一种提高渗碳件表面硬度、控制表面组织分散度的工艺.pdf
涵蓄****09
在线预览结束,喜欢就下载吧,查找使用更方便
相关资料
一种提高渗碳件表面硬度、控制表面组织分散度的工艺.pdf
本发明涉及一种提高渗碳件表面硬度、控制表面组织分散度的工艺,具体步骤为:将工件放入加热炉内升温至650℃,保温2小时;再将升温后的工件升温至800℃,加热炉内碳势CP达到0.4C%,保温2小时;进行渗碳,将再次升温后的工件升温至930℃,控制碳势先为高碳势强渗阶段,后为低碳势扩散阶段,高碳势强渗阶段的碳势CP为1.20C%、渗碳时间为27小时,低碳势扩散阶段的碳势CP为0.75C%、渗碳时间为13小时;将工件快冷到650℃,保温4小时;快冷后的工件进入缓冷坑,降温至750℃,保温5~10min,再次快冷到
提高表面硬度的万向节球壳渗碳工艺.pdf
本发明公开了一种提高表面硬度的万向节球壳渗碳工艺,包括以下步骤:步骤一、选用特定质量百分比组分的渗碳钢材料锻造万向节球壳毛坯;经过正火处理后,进行车、铣加工;步骤二、加热至925℃进行升温排气,升温排气的时间为2.5小时,渗剂的滴加速度为每分钟100滴;步骤三、装炉保持925℃进行保温渗碳,保温渗碳的时间为4小时,渗剂的滴加速度为每分钟210滴;步骤四、保持925℃进行保温扩散,保温扩散的时间为3小时,渗剂的滴加速度为每分钟155滴;步骤五、工件随炉温一同下降至850℃,然后取出万向节球壳工件置于空气中进
简便快速检测钢件渗碳表面硬度的方法及装置.pdf
本发明公开了一种简便快速检测钢件渗碳表面硬度的方法及装置。本发明采用一个硬度与合格齿轮的硬度相同的标准磨头,并设计一套能快速将该标准磨头进行简单、快速的旋转的结构,使标准磨头对被测齿轮进行旋转打磨,通过观察打磨后的样品表面,即可对样品做出是否合格的定性检测,这样的方式无需定量检测,极大的简化了检测的流程,操作简便,快速高效,且可靠性好。本发明的方法简单易行,所采用的装置结构简单,制作成本低,使用效果好。
一种降低套圈渗碳后表面硬度的高温回火工艺.pdf
一种降低套圈渗碳后表面硬度的高温回火工艺,它涉及一种降低套圈渗碳后表面硬度的方法。本发明的目的是要解决现有G13Cr4Mo4Ni4V钢制轴承套圈渗碳后高温回火表面硬度高,不易于车削加工的问题。方法:将钢套圈真空渗碳后在680℃~750℃下回火2h~10h,再随炉冷却或氮气冷却;循环步骤一1次~3次,得到降低表面硬度后的套圈。本发明对钢套圈渗碳后的高温回火工艺进行了改进,解决了套圈渗碳后进行高温回火表面硬度高的问题,本发明将现有技术中钢套圈渗碳后进行高温回火的表面硬度45HRC以上降至37~38HRC,有效
一种弹簧表面渗碳工艺.pdf
本发明公开了一种弹簧表面渗碳工艺,将弹簧毛坯放入到渗碳炉中,然后升温至915‑925