
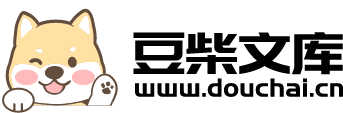
高炉铁口流铁孔道的修复方法.pdf
是笛****加盟
在线预览结束,喜欢就下载吧,查找使用更方便
相关资料
高炉铁口流铁孔道的修复方法.pdf
本发明公开了一种高炉铁口流铁孔道的修复方法,本方法首先在高炉铁口的流铁孔道位置的碳砖上采用开口机钻出通孔,该通孔角度为与水平方向呈7~12度夹角并且向下倾斜;钻孔过程采用干法钻通并且及时取芯以及清灰,钻孔深度为2.5~3米;通孔两侧采用钢板进行支模,采用合适直径的管道贯穿钻出的通孔并且两端分别焊接于通孔两侧的支模上;对管道与通孔之间的间隙采用高流动性、自流性的耐材浇注料进行密实浇注,从而使得管道形成高炉铁口的流铁孔道。本方法彻底解决了铁口出铁和排渣不通畅、煤气漏气、打泥冒泥、出铁喷溅等问题,有效提高了高炉
一种高炉铁口孔道开口方法.pdf
本发明涉及一种高炉铁口孔道开口方法,属于高炉炉前操作技术领域,解决高炉开口过程中铁口易漏、孔道质量欠佳影响高炉正常排放的技术问题。本发明通过分析开口机进给速度、打击、小车进给速度、喷吹压缩空气、喷雾、回拉钻杆操作等对开口过程的不同影响,并综合使用这些开口技术,将孔道易漏点顺利通过,保证铁口孔道的正常工作;减少大氧烧铁口的次数,避免氧气、吹氧管的浪费,同时也减少了烧大氧过程中安全事故的发生;减少了多次使用钻杆和铁棍的成本,减少了在使用钻杆铁棍过程中人机接触的机会,降低了安全事故发生的概率;减少了二次压炮开口
一种新建高炉出铁口孔道浇筑方法.pdf
本本发明公开一种新建高炉出铁口孔道浇筑方法,包括以下步骤:步骤一、在新建高炉的炉缸砌筑完成后,在铁口孔道内安装煤气导出管,并将铁口孔道炉内较低的一端封堵;步骤二、在铁口孔道的另一端设置一下料口;步骤三、将具有自流式性质的高强刚玉浇注料作为填充料通过下料口灌入铁口孔道内,并同时利用振动棒振密实,直至铁口孔道被浇筑满;步骤四、将下料口拆除并浇筑铁口泥套。本发明的新建高炉出铁口孔道浇筑方法,使得成型后的高炉出铁口孔道具有坚固耐用、延长高炉使用寿命以及更加安全可靠的优点。
一种高炉铁口孔道铁水喷溅的处理装置及方法.pdf
本发明公开了一种高炉铁口孔道铁水喷溅的处理装置,包括第二泥炮、以及均设置在所述第二泥炮内且从所述第二泥炮的口部向所述第二泥炮的内部依次设置的水泥炮、无水浆料、第二生产炮泥。本发明还提供了一种高炉铁口孔道铁水喷溅的处理方法,包括:于高炉铁口处获得高炉铁口孔道,通过所述高炉铁口孔道出铁,后使用第一生产炮泥堵住所述高炉铁口孔道;得到高炉铁口孔道铁水喷溅的处理装置;于高炉铁口处获得高炉铁口压浆孔道;将所述高炉铁口孔道铁水喷溅的处理装置堵住所述高炉铁口压浆孔道,后将所述无水浆料烧结固化,实现防止铁水喷溅的目的。可在
一种高炉铁口修复方法.pdf
本发明公开了一种高炉铁口修复方法,其关键改进在于:包括以下步骤:(1)拆除铁口中心线以下的棕刚玉砖和碳砖;拆除范围以铁口中心线为基准左右对称,拆除范围的宽度大于1200毫米,高度大于600毫米,拆除范围自炉皮向内进深大于600毫米;(2)修整铁口内壁;(3)砌筑棕刚玉砖;在拆除棕刚玉砖和碳砖后形成的空腔底部砌筑至少两层棕刚玉砖;(4)安装冷却盘管;在砌筑棕刚玉砖以后的空腔内安装冷却盘管;(5)浇注棕刚玉填料;在安装冷却盘管以后的空腔内浇注棕刚玉填料;(6)炉皮压浆;完成棕刚玉填料浇注以后,在浇注的棕刚玉填