
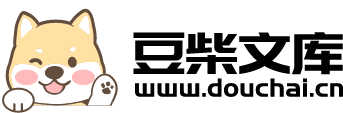
一种转炉循环利用钢包热态铸余渣的方法.pdf
是湛****21
在线预览结束,喜欢就下载吧,查找使用更方便
相关资料
一种转炉循环利用钢包热态铸余渣的方法.pdf
本发明公开了一种转炉循环利用钢包热态铸余渣的方法,属于钢铁冶金技术领域,解决现有技术中铸余渣及其自身余热无法有效利用的问题。本发明的方法包括如下步骤:将钢水浇铸完毕后残留在钢包中的热态铸余渣返回转炉炼钢工序进行循环回收利用;热态铸余渣的碱度为6~8。本发明的方法节能、环保、有效、稳定地利用液态连铸的铸余渣实现了铸余渣热态循环利用,能够降低钢铁料消耗,有效利用炉渣显热,提高冶炼效率,降低炼钢生产成本,提高钢水质量、环保效益明显。
一种钢包铸余渣热态返回转炉利用防止粘包及喷溅的方法.pdf
本发明公开了一种钢包铸余渣热态返回转炉利用防止粘包及喷溅的方法,属于资源综合利用技术领域。本发明将一定量的未经脱硫的铁水投入铁水罐后,将钢包铸余渣倒入铁水罐内,同时加入一定量的压渣材料,一包铸余渣倒完后,再加入一定量的压渣材料,当铁水罐承接的热态铸余渣总量超过铁水重量的65%,或铁水罐料面距离罐口的净空高度小于500mm时,停止继续接受铸余渣。针对于现有技术中存在的问题,本发明拟提供一种钢包铸余渣热态返回转炉利用防止粘包及喷溅的方法,采用控制铁水与铸余渣的混兑比例,调控Fe‑C合金的液相线温度,从而保证铸
一种热态铸余渣直接返转炉的方法.pdf
一种热态铸余渣直接返转炉的方法,其包括如下步骤:1)铁水包准备;2)承接铁水;3)铁水包转运;4)接收铸余渣;5)铸余渣转运;6)铸余渣返转炉。本发明所述方法在回收钢水的同时,将铸余渣转化为转炉渣,后续采用清洁高效的滚筒工艺进行处理,具有显著的经济效益和环保效益。
一种钢包铸余钢和铸余渣的回收利用方法.pdf
本发明公开了一种钢包铸余钢和铸余渣的回收利用方法,属于钢铁冶炼技术领域。它包括将铸余钢和铸余渣装入含有垫底铁水的铁水罐中;所述铸余钢和铸余渣的温度不低于1500℃,所述垫底铁水中的P含量为0.100wt%~0.150wt%,S含量为0.020wt%~0.060wt%。本发明能够实现铸余钢和铸余渣热量的直接回收利用,同时在垫底铁水与铸余钢接触时,铸余渣也进入垫底铁水中,高碱度的铸余渣在搅拌作用下能脱除部分铁水中的有害元素S和P,并减少转炉冶炼的石灰消耗。
一种转炉渣热态循环利用方法.pdf
本发明公开了一种转炉渣热态循环利用方法,转炉出钢过程不控制下渣量,在向钢包内倾倒转炉渣的过程中,不间断地向钢包内渣面加入炉渣还原剂;利用LF电极加热形成的高温区实现炉渣还原剂与炉渣中磷、硅、锰、铁氧化物的化学反应,同时进行底吹搅拌,气体流量为0.04~0.12Nm