
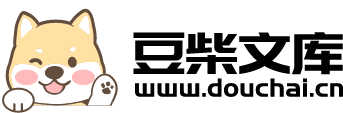
一种转炉冶炼生产系统用副原料料仓自动称量控制方法.pdf
努力****承悦
亲,该文档总共11页,到这已经超出免费预览范围,如果喜欢就直接下载吧~
相关资料
一种转炉冶炼生产系统用副原料料仓自动称量控制方法.pdf
本发明揭示了一种转炉冶炼生产系统用副原料料仓自动称量控制方法及方法,采用吹炼时间基准与氧量基准双基准控制、副原料称量顺序表控制,实现转炉副原料称量全自动控制。本发明根据每炉钢的实际情况形成控制决策,自动制作出称量控制模式,并控制副原料称量机执行,改变了转炉副原料称量采用手动或半自动操作的传统方法;从而将副原料系统操作规范化、标准化、自动化,改善操作人员个体技术水平偏差,有利于提高转炉副原料系统操作的整体水平,稳定转炉生产。
一种转炉合金生产系统的料仓用自动称量控制方法.pdf
一种转炉合金生产系统的料仓用自动称量控制方法,其具体步骤如下所述:1)根据事先确定的合金添加牌号及添加量,建立控制基准分别为,通过时间系统建立吹炼时间基准和通过氧量系统建立吹氧量基准;2)根据吹炼时间基准和吹氧量基准计算并区分称量时间段为,吹炼过程中的称量时间段和出钢中的称量时间段;3)根据获得的吹炼过程中的称量时间段的数据和出钢中的称量时间段的数据,将这两个数据进行称量时间段初步计算,并将计算结果进行人工确认和修订;4)将计算结果输入控制称量机及称量斗,进行自动称量。本发明能称量工艺复杂的铝系合金在内所
一种转炉合金自动称量虚拟料仓控制方法.pdf
本发明公开了一种转炉合金自动称量虚拟料仓控制方法,包括a.根据事先确定的合金添加牌号及添加量,并计算添加增碳剂C‑GR和C‑LN的总量,若增碳剂总量大于0,实施步骤b;b.开设虚拟料仓,相应调整原料仓称量值以保持总称量值不变;c.建立控制基准,分别为通过时间系统建立吹炼时间基准和通过氧量系统建立吹氧量基准;d.构筑吹炼中实体料仓称量模式,若有虚拟料仓,则再构筑吹炼中虚拟料仓称量模式;e.构筑出钢中实体料仓称量模式;f.经人工确定和修订后输入控制称量机和称量斗,进行自动称量。本发明可用于提高转炉合金化自动化
一种向转炉高位料仓上料的自动控制系统和控制方法.pdf
本发明涉及一种向转炉高位料仓上料的自动控制系统,其特征在于,所述控制系统包括综合控制模块;上料时钟控制模块、高位料仓上料量计算模块、上料优先级确定模块、物料堆密度修正模块、上料小车控制模块、地下料场振动给料控制模块、上料量的实时计量模块、上料过程综合控制模块,所述综合控制模块分别连接上料时钟控制模块、高位料仓上料量计算模块、上料优先级确定模块、物料堆密度修正模块以及上料过程综合控制模块,所述上料过程综合控制模块同时连接上料小车控制模块、地下料场振动给料控制模块、上料量的实时计量模块。
一种转炉辅原料上料控制方法及控制系统.pdf
本发明公开了一种转炉辅原料上料控制方法及控制系统,应用于自动控制领域,该控制方法包括:控制各个皮带传输机上的卸料小车定位,以及控制各个所述皮带输送机逐个启动;在各个皮带传输机均处于运行状态后,各个皮带输送机基于预上料编组依次从供料仓获得各个辅原料,传送至对应的要料仓进行上料;在各个辅原料传送至对应的要料仓过程中,监测各个要料仓是否发生断料;在监测到其中一个要料仓发生断料时,将断料仓的上料次序优先插入所述预上料编组中后,继续从供料仓获得辅原料传送至对应的要料仓进行上料。这样就解决了现有转炉冶炼上料控制准确性