
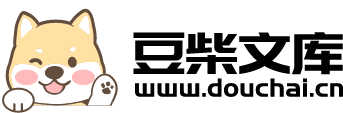
一种铜片氧化方法.pdf
Ch****49
在线预览结束,喜欢就下载吧,查找使用更方便
相关资料
一种铜片氧化方法.pdf
本发明涉及一种铜片氧化方法,将铜片与陶瓷层键合的一面形成特定厚度的氧化层,另一面不形成氧化层。其中,氧化炉内设置有入口、加温区、冷却区以及出口,加温区包括十个温区,各区温度设置如下:一区550℃、二区650℃、三区680℃、四区720℃、五区720℃、六区720℃、七区750℃、八区750℃、九区720℃、十区710℃;氧化炉顶部和底部的进气口处均分别设置有氧气进气管和氮气进气管,氧气的流量设定为38mL/min,氮气的流量设定如下:入口25~35L/min;加温区中一至三区顶部0L/min、四至六区顶部
一种氧化DCB铜片的方法.pdf
本发明公开了一种氧化DCB铜片的方法,涉及覆铜陶瓷基板加工领域,旨在解决铜片氧化不均匀的问题,其技术方案要点是:一种氧化DCB铜片的方法,包括以下步骤:1)选用隧道炉作为氧化设备,在隧道炉的底部和顶部均匀分布加热电阻丝,取压缩空气作为氧化气源,同时保证隧道炉内的空间与外界空气相通;2)将铜片放置在网带的上,逐步进入到隧道炉内进行氧化;3)在隧道炉内设置有十个依次排列的独立温区,每个温区的温度设置为300℃;4)安置在网带上的铜片依次经过上述温区,带速为6.0inch/min,氧化时间15min。本发明的一
一种双层铜片氧化治具及氧化方法.pdf
本发明提供一种双层铜片氧化治具,包括上矩形框架和下矩形框架,上矩形框架和下矩形框架通过两个侧板连接,两个侧板相对设置,两个侧板上均开设有若干通气孔;一种根据所述氧化治具氧化铜片的氧化方法:将两个待氧化铜片分别放置在双层铜片氧化治具的上矩形框架和下矩形框架上,通过传送带进入氧化炉中,双层铜片氧化治具的底部和顶部同时通入氧气,达到上下两层铜片同时氧化效果;设计退火温区及通气设置,平衡上下氛围,达到两层氧化均匀的效果;为改善现有陶瓷覆铜技术中存在陶瓷层和铜层结合不致密、结合强度较低、易鼓包的情况,本发明在氧化后
一种提高铜片氧化层均匀性的氧化炉.pdf
本发明陶瓷覆铜板技术领域,公开了一种提高铜片氧化层均匀性的氧化炉,包括:炉体,包括分别设置在炉体两端的进料口和出料口,进料口和出料口处设置有密封气帘;传送带,用于输送铜片,由进料口到出料口贯穿炉体;多个热电偶,正对传送带安装在炉体内,且沿传送带输送方向依次排布;供氧管道;多个弥散气盒,沿传送带输送方向在炉体内排布,分别与供氧管道连通且在连通处设置有用于控制炉体内气体浓度、流速、流向的气阀;测温热电偶和测氧仪,设置在弥散气盒靠近传送带的一侧;保证了铜片氧化环境的稳定,使铜片表面氧化膜厚度均一。
湿法氧化铜片烧结直接敷铜的方法.pdf
本发明湿法氧化铜片烧结直接敷铜的方法,包括如下步骤:第一步,对铜片进行预先表面处理;第二步,将经过表面处理的铜片放入处理溶液中氧化;第三步,将经过氧化的铜片进行清洗并烘干;第四步,将烘干的铜片放入模具中预弯;第五步,将预弯完毕的铜片放置在陶瓷片上烧结。本发明湿法氧化铜片烧结直接敷铜的方法与高温退火、氧化相比,湿法氧化有利于缩短工序时间、节约能源、降低成本,不需要添加退火炉等设备。与高温退火、氧化相比,湿法氧化生产出来的DBC产品铜面晶粒细小,有利于提高铜片的力学性能,消除传送带痕迹。