
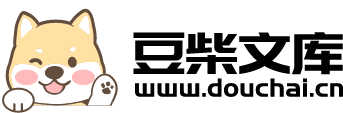
一种排气尾管成型方法.pdf
一吃****海逸
在线预览结束,喜欢就下载吧,查找使用更方便
相关资料
一种排气尾管成型方法.pdf
本发明公开了一种排气尾管成型方法,包括以下:采用上模具、压料机构和下模具进行配合冲压,上模具、压料机构和下模具上分别设有相互匹配的带弧度的冲头、带凹位的定位槽、带内凹弧形成模腔的下模板,把带呈翼形的金属薄片放在位槽,通过冲头向定位槽、下模板冲压,使带呈翼形的金属薄片在带凹位的定位槽、带内凹形成模腔的下模板内成型,形成带弧度的未封口的排气尾管预制件;再采用焊接方式把预制件的缝隙口焊接即可。一次成型,且在定位槽、下模板内成型,形成上、下双凹槽内成型,成型效果好,且易定型。采用通过装置设定进行冲压,省略了多个冲
一种汽车排气尾管角度自动调节系统及方法.pdf
本申请涉及一种汽车排气尾管角度自动调节系统及方法,其包括:排气尾管,排气尾管连接于后处理器上,排气尾管的排气口所扫过的区域为待检区域;排气尾管角度调节机构,其与排气尾管连接,并用于驱使排气尾管旋转,以调整排气尾管的尾气排气口朝向;传感器,其位于待检区域,并用于检测待检区域的目标数据;控制器,其与排气尾管角度调节机构和传感器相连接,并用于接收目标数据,并根据目标数据与阈值的对比结果,控制排气尾管角度调节机构驱使排气尾管旋转。本发明使排气尾管的排气口角度可调,排气尾管的角度调节实现了自动化操作,可以避免排出的
一种汽车排气系统用装饰尾管.pdf
本发明公开了一种汽车排气系统用装饰尾管,内胆上片和内胆下片配合形成内胆的排气通腔,连接架设置在内胆外壁上,外胆套设在内胆外部且通过连接架与内胆的出气端连接,第一安装件和第二安装件安装在内胆上用于将内胆与汽车后保险杠连接,尾片连接在内胆的进气端,且尾片与内胆下片平滑过渡。通过上述优化设计的汽车排气系统用装饰尾管,结构设计合理,通过设计尾片,能够有效隔热,起到美观的效果,并且尾片单独设计,便于加工;此外,通过对安装架的优化设计,大大提高支撑力和定位精度。
一种排气尾管点焊工装.pdf
本发明涉及汽车零部件加工领域,具体为一种排气尾管点焊工装,包括支撑架以及若干个用于对上片体和下片体进行装夹定位的夹具,夹具包括上夹具、铰接件、下夹具以及第一气缸,下夹具和第一气缸均安装于支撑架上,上夹具通过铰接件与下夹具铰接,第一气缸的活塞杆通过铰接件与上夹具之间形成杠杆结构,且上夹具和下夹具上均设有用于进行焊接操作的镂空结构。本发明的结构简单,布局合理,其通过将合在一起的上片体和下片体放置在下夹具上,然后在杠杆结构的作用下,通过控制第一气缸使得上夹具紧压在下夹具上,得以对上片体和下片体进行装夹定位,并从
工程机械排气尾管.pdf
本发明公开了一种工程机械排气尾管,涉及工程机械技术领域,包括有排气管,其特征在于:所述排气管的上部套装有外管,所述外管内设置有一内管,所述内管下端与所述外管下端的封口之间留有间隙,在所述外管内高于所述排气管上端的位置设置有一隔离体,所述内管上端通过隔离体与外管固定连接。本发明提供一种工程机械排气尾管,可以解决工程机械在工作中噪声大的问题。