
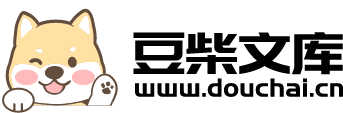
轴管外圆磨削的圆度误差分析及应用.docx
胜利****实阿
在线预览结束,喜欢就下载吧,查找使用更方便
相关资料
轴管外圆磨削的圆度误差分析及应用.docx
轴管外圆磨削的圆度误差分析及应用吴忠东(佛山永力泰车轴有限公司)摘要:本文分析了车轴磨外圆出现圆度超差的原因,指出工件在车中心孔时作为支撑基准的外圆的圆度对中心孔圆度误差影响极大。基准外圆圆度误差通过中心孔间接复映到磨削外圆上,使得磨削外圆圆度超差。通过对基准外圆圆度误差的控制,有效降低了磨削外圆的圆度误差,在生产中取得显著效果。关键词:轴管磨削圆度误差夹持基准中心孔分析1.引言挂车车轴是挂车极其重要的受力零件,直接影响挂车的承载能力和使用寿命。设计上要求对车轴两端轴承位进行磨削加工,并对轴承位的椭圆度作
外圆切入式磨削工件圆度误差实时计算方法.pdf
本发明涉及一种外圆切入式磨削工件圆度误差实时计算方法,首先,采集磨削全过程中的声发射信号,并对该信号进行滤波处理;接着通过傅里叶变换提取所获得信号的谐波频率及对应的振幅;然后通过工件最终轮廓是砂轮对工件每圈叠加加工效果的总和,并结合谐波频率及振幅建立工件轮廓水平展开后的轮廓轨迹方程;最后应用经过变形处理的最小二乘法来计算工件圆度误差。该计算方法对外圆切入磨削过程中工件圆度误差进行实时计算,克服了现有外圆磨削对圆度仪的依赖,提高磨削加工效率,节约生产成本。
用于外圆切入磨削工件圆度误差实时计算方法.pdf
本发明涉及一种用于外圆切入磨削工件圆度误差实时计算方法,先对驻留阶段磨削功率值测定,首先进行一次试加工,记录驻留阶段开始时的第一个功率值及之后的功率值;然后,建立磨削过程轮廓轨迹方程,通过进给阶段和驻留阶段实际材料去除量的变化关系建立磨削过程轮廓轨迹方程;最后,实时计算工件圆度误差,通过工件外圆轮廓极坐标方程可得出任意时刻工件的外圆轮廓,并结合圆度误差最小二乘法求出工件的圆度误差。该计算方法可以对外圆切入磨削过程中任意时刻工件圆度误差进行计算,在计算结果达到圆度误差要求时停止磨削,可提高磨削加工效率,节约
圆度与谐波评价的误差分析.docx
圆度与谐波评价的误差分析圆度与谐波评价的误差分析摘要:圆度与谐波评价是一种常用的几何形状误差评价方法,用于确定物体的圆形度和表面质量。本文对圆度和谐波评价的误差来源进行了详细的分析和讨论,探讨了影响评价准确性的各种误差因素,并给出了相应的解决方法。通过对误差来源和解决方法的研究,可以提高圆度和谐波评价的准确性和可靠性。关键词:圆度,谐波,评价,误差源,解决方法第一节引言圆度和谐波评价是一种常用的几何形状误差评价方法,广泛应用于制造业和测量领域。它可以帮助确定物体是否符合要求的几何形状和表面质量。圆度评价主
刻度环圆度误差分析.docx
刻度环圆度误差分析论文题目:刻度环圆度误差分析摘要:刻度环是一种常见的测量工具,在工业生产和实验中广泛应用。然而,刻度环的制造和使用过程中难免会产生圆度误差,这可能影响到测量结果的准确性。本论文将深入研究刻度环圆度误差的产生原因和影响,并提出针对圆度误差进行分析和校正的方法,以改善刻度环的精度和可靠性。第一章:引言1.1研究背景1.2研究目的和意义第二章:刻度环的基本原理和应用2.1刻度环的定义和结构2.2刻度环的测量原理2.3刻度环的应用领域第三章:刻度环圆度误差的产生原因3.1材料特性对圆度误差的影响