
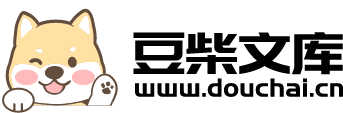
一-、锻造过程质量控制.docx
小琛****82
在线预览结束,喜欢就下载吧,查找使用更方便
相关资料
一-、锻造过程质量控制.docx
、锻造过程质量控制锻造♦什么叫做锻造:在加压设备及工模具)的作用下,使坯料产生局部或全部的塑性变形,以获得一定的几何形状,形状和质量的锻件的加工方法称为锻造。♦锻造的分类:自由锻造只用简单的通用性工具,或在锻造设备上、下砧间直接使坯料变形而获得所需的几何形状及内部质量的锻件。模锻利用模具使毛坯变形而获得锻件的锻造方法.自由锻造的方法镦粗:使毛坯高度减小,横断面积增大的锻造工序.局部镦粗:在坯料上某一部分进行的镦粗.镦粗的过程控制:1。为了防止镦粗时产生纵向弯曲,圆柱体坯料的高度与直径之比不应超过2.5-3
一-、锻造过程质量控制.docx
、锻造过程质量控制锻造♦什么叫做锻造:在加压设备及工模具)的作用下,使坯料产生局部或全部的塑性变形,以获得一定的几何形状,形状和质量的锻件的加工方法称为锻造。♦锻造的分类:自由锻造只用简单的通用性工具,或在锻造设备上、下砧间直接使坯料变形而获得所需的几何形状及内部质量的锻件。模锻利用模具使毛坯变形而获得锻件的锻造方法.自由锻造的方法镦粗:使毛坯高度减小,横断面积增大的锻造工序.局部镦粗:在坯料上某一部分进行的镦粗.镦粗的过程控制:1。为了防止镦粗时产生纵向弯曲,圆柱体坯料的高度与直径之比不应超过2.5-3
一锻造过程质量控制.docx
一、锻造过程质量控制1,锻造◆什么叫做锻造:□在加压设备及工(模具)的作用下,使坯料产生局部或全部的塑性变形,以获得一定的几何形状,形状和质量的锻件的加工方法称为锻造.◆锻造的分类:□自由锻造只用简单的通用性工具,或在锻造设备上、下砧间直接使坯料变形而获得所需的几何形状及内部质量的锻件.模锻利用模具使毛坯变形而获得锻件的锻造方法.□自由锻造的方法镦粗:使毛坯高度减小,横断面积增大的锻造工序.局部镦粗:在坯料上某一部分进行的镦粗.镦粗的过程控制:1.为了防止镦粗时产生纵向弯曲,圆柱体坯料的高度与直径之比不应
321锻造过程质量控制01.pdf
1896192019872006材料加工过程质量控制和管理第三章材料成形的质量控制第二节塑性成形质量控制主要参考书目(1)庞国星.材料加工质量控制.北京:机械工业出版社2011(2)锻件质量分析编写组编著.锻件质量分析.北京:机械工业出版社1983(3)杜忠权.锻件质量控制.北京:航空工业出版社1988(4)吕炎.
锻造过程质量控制知识培训(1).pdf
◆什么叫做锻造□在加压设备及工模具的作用下使坯料产生局部或全部的塑性变形以获得一定的几何形状形.状和质量的锻件的加工方法称为锻造◆锻造的分类□自由锻造只用简单的通用性工具或在锻造设备上、下砧间直接使坯料变形而获得所需的几何形状及内部质量的锻.件.利用模具使毛坯变形而获得锻件的锻造方法□自由锻造的方法镦粗使毛坯高度减小横断面积增大的.锻造工序.局部镦粗在坯料上某一部分进行的镦粗:镦粗的过程控制1.,为了防止镦粗时产生纵向弯曲圆柱体坯料2.5-3,的高度与直径之比不应超过且镦粗前,.坯料端面应平整并与轴心线垂