
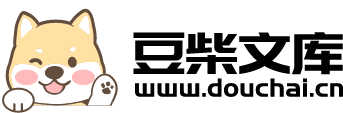
齿轮毛坯等温退火工艺与等温退火生产线.pdf
小新****ou
在线预览结束,喜欢就下载吧,查找使用更方便
相关资料
齿轮毛坯等温退火工艺与等温退火生产线.pdf
本发明涉及一种批量生产的齿轮锻造毛坯的热处理工艺与一条相应的热处理生产线。本发明免除了对齿轮毛坯的整体重结晶加热,不论是采用本发明的锻造余热等温退火工艺或是毛坯冷却后实施的等温退火都能使齿坯稳定地获得具有优越切削性能的金相组织和预期的硬度值。
一种等温退火节能炉及其等温退火方法.pdf
本发明提供一种等温退火节能炉,包括炉体,还包括:进料预热室,用于预加热进入炉体的工件;加热恒温室,用于加热在进料预热室中预加热后的工件并使工件保持恒温;强制冷却室,用于冷却在加热恒温室中加热后的工件;等温室,用于保持在强制冷却室中冷却后的工件的温度;出料热交换室,用于对在等温室中保持温度后的工件降温;滚道,用于供工件进出炉体及在炉体中运动;热交换系统,用于将出料热交换室中工件散发的余热输送到进料预热室以预加热工件。本发明通过设置余热交换的热交换系统,单位吨生产能耗较现行指标降低40%以上,且工时缩短。
18CrNiMo7-6齿轮轴锻件预热处理等温退火工艺.pdf
本发明提供了一种18CrNiMo7‑6齿轮轴锻件预热处理等温退火工艺,属于金属材料热处理领域,其包括步骤:a、预加热处理,将18CrNiMo7‑6风电齿轮轴锻件,预热处理选用台车式热处理炉,以小于150℃/h的加热速度加热到930~950℃;b、保温处理,按锻件截面尺寸1.5min/mm的计算930~950℃保温时间,保温结束打开炉门,将台车开出;待锻件表面冷却到600~650℃,将台车开入且关门,再加热到750℃保温1小时;c、冷却处理,以小于10℃/h的速度炉冷到550℃出炉空冷。本发明提供的一种18
CMOS器件的等时、等温退火效应.pdf
一种免等温退火低碳齿轮钢的生产方法.pdf
本发明涉及一种免等温退火低碳齿轮钢的生产方法,工艺流程为转炉初炼→精炼炉精炼→RH炉真空脱气→连铸方坯→高温加热→粗轧→中轧→精轧→高温圆钢穿水→钢材入缓冷坑缓冷。齿轮钢的金相组织为铁素体和珠光体,铁素体条带宽度≤20um,奥氏体晶粒度为7‑9级,产品硬度≤170HBW,产品全截面的硬度极差≤10HBW,产品纵向带状组织≤2.0级。化学成分按重量百分比为C:0.17~0.20%,Si:≤0.07%,Mn:0.70~0.90%,Cr:1.15~1.25%,P:≤0.010%,S:0.023~0.040%,A