
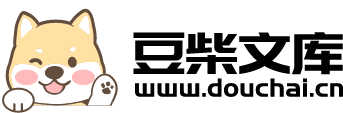
一种高温合金薄壁机匣数控车加工方法.pdf
佳晨****ng
在线预览结束,喜欢就下载吧,查找使用更方便
相关资料
一种高温合金薄壁机匣数控车加工方法.pdf
一种高温合金薄壁机匣数控车加工方法,其特征在于:在编制数控加工程序时,采用循环程序和轮廓程序两种方式结合,在循环程序中直接设定切削深度,机床操作者不能随意改动;最后一刀采用轮廓程序,保证零件的粗糙度和加工精度;数控程序走刀路线:在循环程序中采用对称切削的新式加工方法,先车加工外圆再对称车加工内孔;先车加工安装边上方再对称车加工安装边下方;合理的设置切削余量。本发明的优点:本发明所述的高温合金薄壁机匣数控车加工方法,进行机匣、叶盘类零件的数控车削加工,保证了零件车削加工的尺寸及精度,缩短零件加工时间,降低加
高温合金机匣的环槽加工方法.pdf
本发明公开了一种高温合金机匣的环槽加工方法,环槽为扇形结构,包括以下步骤:粗加工,在高温合金机匣上依据设计需求确定加工区域,采用钻削对加工区域进行垂直钻孔,以去除大部分加工余量;第一次半精加工,采用立铣刀对钻削后的区域进行铣削加工,铣削至环槽的槽底预留2mm和槽壁单边预留0.2mm的加工余量;第二次半精加工,将球头铣刀伸入到环槽内进行铣削加工,铣削至环槽的槽底;精加工,采用球头铣刀对环槽进行精加工,获得环槽。本发明的高温合金机匣的环槽加工方法,依据不同的加工方式,采用不同的刀具,对环槽不同部位有针对性的加
一种薄壁带涂层机匣加工方法.pdf
一种薄壁带涂层机匣加工方法,机匣壳体的加工路线安排,在将精车工序中将内部重要尺寸、涉及后续装配的尺寸留0.3mm~0.5mm余量,待喷涂工序结束后再进行剩余余量的加工,有效的抵消喷涂工序中吹砂、喷涂工序对壳体的冲击;喷涂工序前在内型面或装配T型槽内安装随行的橡胶材料填充物,在喷涂工序进行应用;抵消喷涂、吹砂工步对零件的冲击力;对保证型面的余量均匀,控制最终状态下零件的变形量。本发明的优点:整个加工流程进行了调整优化,节省了用于装配的潜修工作量70%以上,同时避免了后续涂层脱落、掉块的情况,涂层的使用寿命提
高温合金机匣加工工艺论文.docx
高温合金机匣加工工艺论文1主要零件制造难点分析和加工工艺1.1导向器机匣主要难点分析和加工工艺导向器机匣结构形式为薄壁环型机匣其主要加工工艺和难点是机匣上叶型孔薄壁处的数控车加工和叶型孔的激光切割加工。加工时零件易椭圆变形薄壁处出现弧形变形加工表面振纹大表面粗糙。通过合理安排粗精加工余量和走刀路线多次对数控程序进行调整优化加工参数满足了尺寸要求。薄壁处加工方案是:先对内形进行粗加工并且为内形薄壁处留出0.5mm的加工余量这解决了在精加工时的变形和振纹对外形
大型薄壁铝合金机匣外环加工工艺.docx
大型薄壁铝合金机匣外环加工工艺大型薄壁铝合金机箱外环加工工艺摘要:随着社会的进步和科技的发展,大型薄壁铝合金机箱的需求也越来越大。然而,薄壁铝合金机箱的加工工艺相对较为复杂,需要在保证产品质量的前提下提高生产效率。本文主要介绍了大型薄壁铝合金机箱外环的加工工艺,并详细分析了各个环节的关键点和注意事项。关键词:薄壁铝合金机箱、加工工艺、外环、关键点、注意事项一、引言大型薄壁铝合金机箱是一种常见的工业产品,广泛应用于电力、电子、通信等领域。在制造过程中,大型薄壁铝合金机箱的外环加工工艺是非常重要的一环。二、大