
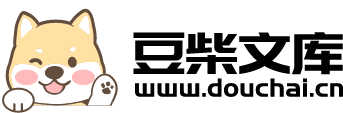
铝合金压铸件常见缺陷及改进方案.docx
快乐****蜜蜂
在线预览结束,喜欢就下载吧,查找使用更方便
相关资料
铝合金压铸件常见缺陷及改进方案.doc
压铸件缺点缺点特征及检验方法产生原因改进方案(提议)1、气孔(空气孔、气眼)特征:压铸件内部(加工面)较为光滑孔洞。检验方法:定点、定面试加工或X光探测,判断是否影响成品质量。浇口位置选择和导流形状不妥,造成金属液进入型腔产生正面撞击和产生旋涡。浇道形状设计不良。压室充满度不够。内浇口速度太高,产生湍流。排气不畅。模具型腔位置太深。涂料过多,填充前未燃尽。炉料不洁净,精炼不良。机械加工余量太大(0.5以上)。1)选择有利于型腔内气体排除浇口位置和导流形状,防止金属液先封闭分型面上排溢系统。直浇道喷嘴截面积
铝合金压铸件常见缺陷及改进方案.docx
1、气孔(空气孔、气眼)特征:压铸件内部(加工面)较为光滑的孔洞。检查方法:定点、定面试加工或X光探测,判断是否影响成品质量。1)浇口位置选择和导流形状不当,导致金属液进入型腔产生正面撞击和产生旋涡。2)浇道形状设计不良。3)压室充满度不够。4)内浇口速度太高,产生湍流。5)排气不畅。6)模具型腔位置太深。7)涂料过多,填充前未燃尽。8)炉料不干净,精炼不良。9)机械加工余量太大(0.5以上)。1)选择有利于型腔内气体排除的浇口位置和导流形状,避免金属液先封闭分型面上的排溢系统。2)直浇道的喷嘴截面积应尽
铝合金压铸件常见缺陷及改进方案.doc
1、气孔(空气孔、气眼)特性:压铸件内部(加工面)较为光滑的孔洞。检查方法:定点、定面试加工或X光探测,判断是否影响成品质量。1)浇口位置选择和导流形状不妥,导致金属液进入型腔产生正面撞击和产生旋涡。2)浇道形状设计不良。3)压室充满度不够。4)内浇口速度太高,产生湍流。5)排气不畅。6)模具型腔位置太深。7)涂料过多,填充前未燃尽。8)炉料不干净,精炼不良。9)机械加工余量太大(0.5以上)。1)选择有助于型腔内气体排除的浇口位置和导流形状,避免金属液先封闭分型面上的排溢系统。2)直浇道的喷嘴截面积应尽
铝合金压铸件常见缺陷及改进方案样本.doc
1、气孔(空气孔、气眼)特性:压铸件内部(加工面)较为光滑孔洞。检查办法:定点、定面试加工或X光探测,判断与否影响成品质量。1)浇口位置选取和导流形状不当,导致金属液进入型腔产生正面撞击和产生旋涡。2)浇道形状设计不良。3)压室布满度不够。4)内浇口速度太高,产生湍流。5)排气不畅。6)模具型腔位置太深。7)涂料过多,填充前未燃尽。8)炉料不干净,精炼不良。9)机械加工余量太大(0.5以上)。1)选取有助于型腔内气体排除浇口位置和导流形状,避免金属液先封闭分型面上排溢系统。2)直浇道喷嘴截面积应尽量比内浇
铝合金压铸件常见缺陷及改进方案[最终版].pdf