
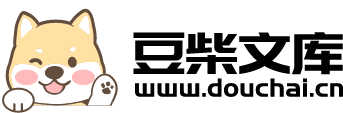
涡轮叶片化学去除渗铝层的方法.pdf
光誉****君哥
在线预览结束,喜欢就下载吧,查找使用更方便
相关资料
涡轮叶片化学去除渗铝层的方法.pdf
本发明属于化学热处理领域,特别是涉及一种涡轮叶片化学去陈渗铝层的方法。该方法包括以下步骤:(1)吹砂,去除所述涡轮叶片表面的积碳和氧化膜;(2)除油;(3)绝缘;(4)去渗铝层,把高温合金钢零件放入去渗铝层溶液,反应时间为1.5小时~2小时,所述去渗铝层溶液由硝酸、氢氟酸和铬酐组成,所述硝酸含量为110ml/l~130ml/l,所述氢氟酸的含量为10ml/l~12ml/l,所述铬酐含量为8~10g/l;(5)中和,把叶片放入碳酸钠溶液中进行中和;(6)清洗,清洗叶片去渗铝层后表面产生的挂灰;(7)去绝缘层
一种渗铝硅料浆及制备涡轮叶片表面铝硅渗层的方法.pdf
本发明属于化学气相沉积技术,涉及一种渗铝硅料浆及制备涡轮叶片表面铝硅渗层的方法。本发明的高硅含量渗铝硅料浆由渗剂和粘结剂组成,渗剂为纯铝粉和金属硅粉,粘结剂为丙酮、乙酰丙酮和硝化纤维素。本发明制备涡轮叶片表面铝硅渗层的步骤是:配制渗铝硅料浆;涡轮叶片表面清理;涂覆渗铝硅料浆;渗铝硅料浆干燥;形成铝硅渗层;清理涡轮叶片;铝硅渗层扩散。本发明提出了一种高硅含量渗铝硅料浆及制备涡轮叶片表面铝硅渗层的方法,满足航空发动机研制的需要。
航空发动机涡轮叶片气相渗铝工艺.docx
航空发动机涡轮叶片气相渗铝工艺航空发动机的性能和效率取决于多个因素,其中一个重要因素就是涡轮叶片的质量和性能。为了提高发动机的性能,工程师们一直在寻找新的材料和加工工艺。其中,涡轮叶片的气相渗铝工艺是一种常用的方法,它可以显著提高叶片的耐热性和耐腐蚀性能。本篇论文将详细介绍航空发动机涡轮叶片气相渗铝工艺的原理和应用。涡轮叶片是航空发动机中最关键的部件之一,它承受着高温高压工作环境下的巨大压力。因此,叶片的材料和加工工艺必须具备卓越的耐热和耐腐蚀性能。传统上,涡轮叶片采用镍基高温合金作为材料,这类材料具有较
渗铝工艺对涡轮叶片表面冶金缺陷荧光显示的影响分析.docx
渗铝工艺对涡轮叶片表面冶金缺陷荧光显示的影响分析渗铝工艺对涡轮叶片表面冶金缺陷荧光显示的影响分析摘要:涡轮叶片是汽车发动机中的关键部件之一,对其表面冶金缺陷进行有效的检测和分析对于保障发动机的可靠运行至关重要。本文主要研究了渗铝工艺对涡轮叶片表面冶金缺陷荧光显示的影响。首先介绍了涡轮叶片的工作原理和常见的冶金缺陷类型,然后详细分析了渗铝工艺对涡轮叶片表面冶金缺陷的影响机理,并探讨了荧光显示在冶金缺陷检测中的应用前景。实验结果表明,渗铝工艺可以显著改善涡轮叶片表面冶金缺陷的荧光特性,提高缺陷检测的准确性和灵
基于系统工程的高压涡轮叶片内腔渗层正向设计.docx
基于系统工程的高压涡轮叶片内腔渗层正向设计高压涡轮是航空发动机中一个重要的组件,其工作在高温高压的环境下,需要能够承受极高的系统压力和热负荷。内腔渗层是一种常用的保护涂层,可以降低高温气流对叶片内部的冷却通道壁面的侵蚀,从而延长叶片的使用寿命。因此,如何正向设计高压涡轮叶片内腔渗层就成为了一个非常重要的研究方向。本文将基于系统工程的方法,对高压涡轮叶片内腔渗层正向设计的研究进行探讨。首先,我们将从设计需求入手,详细介绍设计目标和考虑因素。然后,我们将介绍设计过程并分析其各个环节。最后,我们将讨论如何评估设