
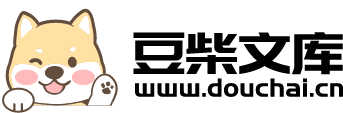
油气悬挂缸活塞杆断裂成因研究.docx
快乐****蜜蜂
在线预览结束,喜欢就下载吧,查找使用更方便
相关资料
油气悬挂缸活塞杆断裂成因研究.docx
油气悬挂缸活塞杆断裂成因研究标题:油气悬挂缸活塞杆断裂成因研究摘要:活塞杆断裂是油气悬挂系统中一种常见的故障,它可能导致车辆运行不稳定、悬挂系统失效甚至是事故的发生。本论文通过分析和研究油气悬挂缸活塞杆断裂的成因,旨在揭示其内在机理,为预防和解决活塞杆断裂问题提供一定的理论参考。一、引言二、活塞杆断裂的现象和影响2.1活塞杆断裂的现象2.2活塞杆断裂的影响三、活塞杆断裂的成因分析3.1疲劳断裂3.2过载断裂3.3动态载荷断裂3.4过热断裂3.5其他因素四、实验与模拟研究4.1活塞杆断裂实验4.2活塞杆断裂
一种油气悬挂缸.pdf
本发明提供了一种油气悬挂缸,包括电缆线,电缆线通过活塞杆连接电磁活塞,电磁活塞的两端充满磁流变液,磁流变液通过电磁活塞在电磁活塞两侧进行流动,活塞将左侧的磁流变液与右侧的氮气隔开,活塞杆与车轮部分连接,缸体与车架部分连接。本发明的目的在于克服上述已有技术的不足,提供一种新型油气悬挂缸用于主动悬架系统中,通过液压控制和磁流变液控制技术,使其同时具有调整车辆底盘离地高度和变阻尼功能,拓展了悬架系统的功能,提高了车辆底盘对不同路况的适应性。
双活塞杆油气弹簧缸.pdf
本发明提出了双活塞杆油气弹簧缸,包括两个油气弹簧缸,两个油气弹簧缸背对设置构成串联结构;所述油气弹簧缸的活塞杆上有单向阀,活塞上有阻尼孔;一个油气弹簧缸内充有高压氮气,一个油气弹簧缸内充有低压氮气。采用本发明,当空载荷和低载荷时,充有低压氮气的油气弹簧缸压缩,因充有高压氮气的油气弹簧缸内充气压力高,相当于刚性体,只有充有低压氮气的油气弹簧缸一端的单向阀和阻尼孔完成弹性体和减振器的作用,当载荷达到一定值时,充有低压氮气的油气弹簧缸的剩余缓冲行程变短,缓冲效果变差,而充有高压氮气的油气弹簧缸开始压缩,两个油气
液压缸活塞杆断裂原因分析.docx
液压缸活塞杆断裂原因分析液压缸活塞杆是液压系统中的核心部件,具有承受液压压力和作用力、传递能量的重要作用。然而,在长期使用过程中,液压缸活塞杆可能会出现断裂现象,给生产和工作带来不良影响。因此,在分析液压缸活塞杆断裂原因的基础上,针对性地制定措施,有助于提高液压系统的整体安全性和可靠性。一、液压缸活塞杆断裂现象液压缸活塞杆的断裂是指在使用过程中,活塞杆的某个部位(多为杆身)或连接头突然断裂的现象,通常会伴随着“啪”的一声声响。此时,活塞杆的移动会变得卡顿或者彻底停止,导致液压系统失效。一旦出现液压缸活塞杆
重载矿用自卸车油气悬挂缸.pdf
本发明涉及一种油气悬挂设备。本发明所述的重载矿用自卸车油气悬挂缸,包括中空的杆筒和缸筒,杆筒和缸筒内腔连通,并且外壁围成一个环形腔,该环形腔与杆筒和缸筒的内腔均连通。本发明的油气悬挂缸的输出力特性、刚度特性和阻尼特性优良,用于车辆的悬挂系统中能对车辆的动力学性能有着极佳的促进作用。