
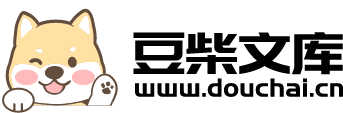
一种离心泵叶轮铸造工艺.pdf
雨星****萌娃
在线预览结束,喜欢就下载吧,查找使用更方便
相关资料
一种离心泵叶轮铸造工艺.pdf
本发明公开了一种离心泵叶轮铸造工艺,其核心为根据模壳进行浇注的过程,所述模壳具有与待铸造叶轮轴孔对应的中心孔,以使叶轮轴孔不铸出;其特征在于:所述模壳中心孔内壁沿圆周均匀设有2‑4道轴向的筋条,以使浇注时形成中心柱状直浇道和与中心柱状直浇道连为一体的2‑4道分流内浇道,所述分流内浇道由相邻两筋条之间的区域在浇注时形成。本工艺能够保证精密铸造过程中壳型形状尺寸稳定,进而减少浇铸时叶轮变形收缩,提高叶轮成品合格率,提高离心泵效率与使用寿命。
离心泵叶轮砂型铸造工艺的分析和改进.pptx
汇报人:/目录0102离心泵叶轮砂型铸造工艺简介离心泵叶轮砂型铸造工艺流程离心泵叶轮砂型铸造工艺的应用范围03离心泵叶轮砂型铸造工艺的优缺点离心泵叶轮砂型铸造工艺的改进方向离心泵叶轮砂型铸造工艺的未来发展趋势04优化铸造材料和配方改进铸造设备和工艺参数提高铸造工人的技能和素质加强生产过程的质量控制和检测05改进前后铸造质量的对比分析改进前后生产效率和能耗的对比分析改进前后产品性能和市场反馈的对比分析06某企业离心泵叶轮砂型铸造工艺改进案例介绍某企业离心泵叶轮砂型铸造工艺改进措施和实施过程某企业离心泵叶轮砂
一种叶轮铸造工艺及叶轮.pdf
本发明涉及铸造技术领域,具体而言,涉及一种叶轮铸造工艺及其叶轮,一种叶轮铸造工艺,包括:采用型芯熔模铸造叶轮型壳;将所述熔模铸造步骤中的型芯用作所述叶轮铸造时叶轮型壳的型芯;所述叶轮型壳以低压铸造工艺形成所述叶轮,一种叶轮,叶轮采用上述铸造工艺铸造而成,本发明中的叶轮通过陶瓷型铸造、熔模铸造和低压铸造结合起来,能够解决叶轮铸造过程中金属液充注不足问题,降低叶轮气孔、疏松现象的产生。
一种高精密铸造半开式离心泵叶轮.pdf
离心泵广泛应用于石油化工、锅炉给水、航空航天等领域,而离心泵的效率就是离心泵的重要指标。有后盖板的叶轮称为半开式叶轮,它的效率在闭式叶轮和开式叶轮之间,可用于高速泵中,叶轮前可装有诱导轮,半开式叶轮主要适用于清水离心泵主要考虑高效率和高汽蚀性能就足够了。本发明公开了一种高精密铸造半开式离心泵,包括离心泵的后盖板,后盖板上有若干叶片,叶片形状呈后弯式,叶片以一定的安放角度,半开式叶轮制造难度较小、成本较低、且适应性强、近年来在炼油化工用离心泵中应用逐渐增多、并用于输送清水和近似清水的液体。
一种耐腐蚀叶轮铸造工艺.pdf
本发明公开一种耐腐蚀叶轮制造工艺,具体选用铝材作为压型模材料,直径300mm以下采用铝棒料做模具材料,直径300mm以上采用生铝做模具材料,粘浆采用硅熔胶,压制环境温度22-26℃,压制温度56-60℃,压制压力0.3-0.6MPa,撒砂原料用100-120目锆砂,脱蜡采用高压蒸汽脱蜡,型壳焙烧在950-1050℃范围内进行,合金溶化及浇注采用316、304不锈钢,其浇注温度为1580-1620℃。本工艺提高了叶轮表面光滑度、减小了材料收缩及型壳的变形,提高了叶轮的耐腐蚀性能。