
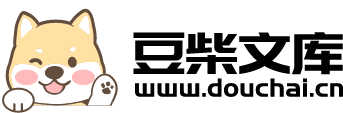
一种铝合金轮毂强力旋压加工成形方法及脱模机构.pdf
俊凤****bb
在线预览结束,喜欢就下载吧,查找使用更方便
相关资料
一种铝合金轮毂强力旋压加工成形方法及脱模机构.pdf
本发明公开了一种铝合金轮毂强力旋压加工成形方法及脱模机构,脱膜机构包括芯模结构,所述芯模结构包括内芯膜和套接于内芯膜外的外芯模,所述脱模机构还包括用于与受力沿径向移动的外芯模锁紧固定的禁锢块和用于推动芯模结构运动且带动外芯模脱离禁锢块的限位伸缩机构。加工成型方法包括通过尾顶将板料顶至芯模结构进行固定,使内芯膜被挤压,外芯模受力沿径向移动至与禁锢块配合锁定;旋转芯模结构,带动尾顶和板料旋转;通过多轮旋压工艺使轮毂成形。本发明解决了复杂截面轮毂旋压成形后脱模困难的问题,脱模原理简单,通用性强。
汽车铝合金轮毂强力旋压成形工艺研究.docx
汽车铝合金轮毂强力旋压成形工艺研究汽车铝合金轮毂强力旋压成形工艺研究摘要:随着汽车工业的快速发展,轮毂作为汽车重要的组件之一,对其性能和质量要求也越来越高。铝合金轮毂具有重量轻、强度高、耐腐蚀等优点,在汽车制造中得到越来越广泛的应用。本文以汽车铝合金轮毂的强力旋压成形工艺为研究对象,通过实验和数值模拟的方法,探讨了铝合金轮毂强力旋压成形过程中的工艺参数对成形过程和成形品质的影响,为提高铝合金轮毂的生产效率和质量提供了一定的理论依据。关键词:汽车铝合金轮毂,强力旋压,成形工艺,数值模拟,工艺参数第1章引言1
一种铸旋铝合金轮毂轮辋旋压成形方法.pdf
本发明公开了一种铸旋铝合金轮毂轮辋成形方法,即轮毂的轮辐和内轮缘为铸态,轮辋中间为旋压态组织的特殊旋压复合加工方法。它能够保持内轮缘处的性能、强度及铸态组织不被破坏,能够有效地提高铸旋轮毂在内轮缘处的抗冲击能力,防止径向冲击时铸旋轮毂内轮缘开裂,并提高轮辋旋压组织的性能,利于轮辋减薄,实现轮辋的轻量化。
汽车铝合金轮毂强力旋压成形工艺研究的中期报告.docx
汽车铝合金轮毂强力旋压成形工艺研究的中期报告该篇中期报告主要介绍了汽车铝合金轮毂强力旋压成形工艺的研究进展情况,包括研究背景、研究目的、研究内容,以及采用的研究方法和初步实验结果。研究背景:汽车轮毂作为车辆外观的重要组成部分,除了美观外还必须具备优秀的安全性和性能,其中材料的选择和成形技术的应用起着至关重要的作用。随着轮毂的功能越来越多元化、复杂化,传统的成形技术已经难以满足设计要求和市场需求,因此需要寻求新的成形工艺。研究目的:本研究旨在探索汽车铝合金轮毂强力旋压成形工艺,并研究其成形特点、成形规律和工
一种铝合金轮毂旋压成形加工工艺润滑剂组合物.pdf
本发明公开了一种铝合金轮毂旋压成形加工工艺润滑剂组合物,采用基础油MVI,配合多种复合添加剂。包括:抗氧剂、金属减活剂、油性剂、摩擦改进剂、极压剂、抗磨剂、抗泡剂、缓蚀剂、催冷剂、防锈剂。本发明的组合物具有良好的极压抗磨减摩性、抗氧化性、热氧化安定性、剪切安定性、冷却性、流动性、清冼性、低挥发性、低烟雾性、防锈性,确保加工部件的表面质量及加工精度。