
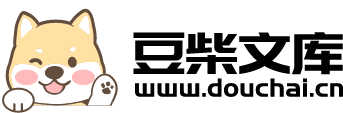
涡轮增压器壳的铸造工艺.pdf
猫巷****忠娟
在线预览结束,喜欢就下载吧,查找使用更方便
相关资料
涡轮增压器壳的铸造工艺.pdf
本发明涉及一种涡轮增压器壳的铸造工艺,其特征在于包括如下步骤:1)制备砂芯及砂型;2)组装、烘干;3)熔炼及球化处理;5)浇注;6)清理检验。本发明通过对铸造型砂及铸造工艺的改进,减少缩孔、缩松、夹砂及气泡等铸造缺陷的产生,提高铸件的成品率和铸件的力学性能,降低铸件成本。
一种用于涡轮增压器涡轮壳的低压铸造工艺.pdf
本申请涉及一种用于涡轮增压器涡轮壳的低压铸造工艺,应用在低压铸造的领域。其包括准备步骤,准备用于铸造的上模具、下模具和砂芯;预处理步骤,在上模具、下模具和砂芯的表面涂覆涂料形成涂层,组装上模具、下模具和砂芯,形成模具整体,将模具整体的注入口与铸造装置的供料管连通;铸造步骤,向铸造装置充气增压,使熔融物料进入模具整体中,持续充气增压,充气增压完成后铸造装置中的泄压组件动作,断开供料管与模具整体的连接,供料管泄压,脱模步骤,分离上模具和下模具,得到铸件。本申请具有不会拉低保持炉中的温度,提升铸造加工效率的效果
一种用于涡轮增压器涡轮壳的低压铸造工艺.pdf
本发明涉一种用于涡轮增压器涡轮壳的低压铸造工艺,包括如下步骤:a、制造上、下模壳;b、制造砂芯组件;c、进行上涂料工艺;d、组装,制作完成模具;e、对合金进行熔炼;f、采用低压铸造的方式对所述铸型进行浇铸;g、等铸件凝固冷却后开箱清理,得到涡轮壳铸件。用该涡轮增压器涡轮壳的低压铸造工艺生产出来的涡轮增压器涡轮壳机械性能高,使用寿命长,金属利用率高,铸造成本低,降低能耗,符合国家对降低单位能耗的政策。
AlSi7Mg涡轮增压器压壳铸造缺陷预测及工艺优化.docx
AlSi7Mg涡轮增压器压壳铸造缺陷预测及工艺优化一、引言随着现代工业的发展,汽车、航空、船舶等交通工具的性能越来越高、要求越来越苛刻,涡轮增压器作为一种能够提高发动机功率、增加燃油经济性和降低排放的装置,应用越来越广泛。涡轮增压器的压壳作为其重要组成部分之一,承载着由增压器产生的高压气体,其质量问题会严重影响整个涡轮增压器的运行效果和寿命。因此,对于涡轮增压器压壳铸造缺陷及工艺优化进行预测和改进是非常重要的。二、涡轮增压器压壳的铸造缺陷涡轮增压器压壳铸造缺陷主要包括气孔、疏松、夹渣、缩孔等。其中,气孔是
铸钢涡轮增压器壳体的铸造工艺.docx
铸钢涡轮增压器壳体的铸造工艺铸钢涡轮增压器壳体的铸造工艺摘要随着现代引擎的发展,涡轮增压器作为一项重要的技术装备,被广泛应用于汽车和船舶等领域。其中,铸钢涡轮增压器壳体作为涡轮增压器的重要组成部分之一,其质量和性能直接影响整个涡轮增压器的工作效果。本文将探讨铸钢涡轮增压器壳体的铸造工艺以及其对产品质量和性能的影响,为铸造工艺的优化提供参考。第一章引言1.1研究背景涡轮增压器是指利用废气能量来压缩空气,以增加进气量,提高汽车发动机输出功率和扭矩的一种设备。铸钢涡轮增压器壳体是涡轮增压器的主要组成部分之一,其