
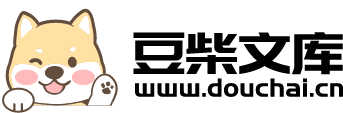
一种基于单目视觉的砂石骨料装车视觉系统及其控制方法.pdf
元容****少女
在线预览结束,喜欢就下载吧,查找使用更方便
相关资料
一种基于单目视觉的砂石骨料装车视觉系统及其控制方法.pdf
本发明公开了一种基于单目视觉的砂石骨料装车视觉系统及其控制方法,包括视觉模块、系统控制模块、系统执行模块、实时图像分析模块和视觉反馈控制模块。本发明利用实时图像分析方法,通过工业相机在图像中检测出卸料口下方一定范围内的料堆轮廓线,结合视觉系统标定结果得到与目标料位的实际偏差,再根据一定的控制律计算出消除该偏差所需的卸料闸门开度,并据此对卸料闸门的开度进行实时调节。通过本发明提供的装车系统和方法能够取得更高的作业效率,在尽可能短的时间内实现平稳装车,同时避免随着车厢料位越来越高或剩余容积越来越小导致的撒料情
基于视觉的单目SLAM方法研究.docx
基于视觉的单目SLAM方法研究摘要:单目SLAM(SimultaneousLocalizationandMapping)是一种基于视觉的定位与建图技术,在无人驾驶、增强现实、机器人导航等领域具有重要应用。本文综述了基于视觉的单目SLAM方法的研究进展,主要包括特征点法、直接法和深度学习方法。特征点法通过检测和描述特征点的位置和外观来进行定位和建图,是最常用的方法之一;直接法通过直接匹配像素的亮度信息来估计相机的位姿,避免了特征提取和匹配的过程;深度学习方法将深度估计任务与SLAM任务结合,通过神经网络学习
基于激光视觉的化肥装车系统及方法.pdf
本发明提供基于激光视觉的化肥装车系统及方法,属于化肥装车技术领域,以解决目前的装车装置装料时,由于需要司机全程盯着料车车斗内的化肥盛放量情况,从而使得整个装车过程中费时费力,且装车漏斗漏料量不可灵活调控的问题,包括:装车漏斗;所述装车漏斗底部设有流量调节装置,且流量调节装置上部位于装车漏斗前侧设有敲击机构,装车漏斗前侧下部设有高度调节组件;所述角度调节组件上安装有2D相机。本发明通过2D相机、图像采集卡和工业计算机的配合,使装车漏斗的下料量得到实时控制,从而使得整个装料过程,司机无需全程盯着料车车斗内的化
一种基于视觉的全自动港口吊装车系统及控制方法.pdf
本发明公开了一种基于视觉的全自动港口吊装车系统及控制方法,包括吊装车和行道,所述吊装车包括控制器、底部的轮子和位于底部的识别器,所述识别器采集口向下设置,所述行道包括两条白线和设置在白线边上的二维码,所述识别器采集白线和二维码的信息并传输给控制器,所述控制器依据识别器采集的信息控制吊装车的运动轨迹和启停,所述吊装车上部设有平台,平台的下表面设有采集装货区域图像的摄像头。采用本发明的技术方案,可以实现全自动码头货车的行驶吊货装货操作,节约了人力物力,并且精度高,操作及时准确。
基于全景视觉的单目SLAM系统的开题报告.docx
基于全景视觉的单目SLAM系统的开题报告1.题目背景随着移动机器人技术的快速发展,SLAM技术已经逐渐成为机器人导航、自主探索、环境构建等重要的基础技术。在SLAM技术中,单目SLAM是最具有前景的一个分支,因为它不需要复杂的硬件配置,只需要一台传统的单目相机即可实现立体视觉的效果。然而,由于单目相机的深度感知信息少,难以确定摄像机在三维空间的位置和姿态,单目SLAM产生的误差较大。全景相机具有对周围环境进行全方位感知的能力,能够提供更多的景深信息,有效改善单目SLAM的精度。目前已有一些研究者尝试基于全