
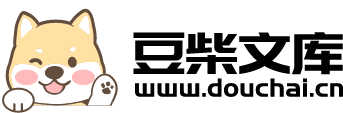
船体曲面成形综述.doc
sy****28
在线预览结束,喜欢就下载吧,查找使用更方便
相关资料
船体曲面成形综述.doc
船体曲面成形工艺综述【关键词】成形加工;双曲度;船体外板船体外板的成形加工一直是船体制造中最为复杂的工序之一,随着船舶制造业的蓬勃发展,现在的加工技术以及加工设备已经不能满足造船行业的要求,需要在原有的板材成形技术基础上革新出一种新的成形技术。1传统成形方法多年来,国内外船厂对曲面分段中的双曲度船体外板加工,一直是采用人工操作,即水火弯板。通常是先使用辊板机或油压机对板材进行横向曲度的弯曲加工成形,然后再在纵向上使用水火弯板技术进行水火线加热,实现纵向曲度弯曲成形。加工过程要靠样板或样箱进行对比和校验[1
船体板冷压成形的残余应力研究的综述报告.docx
船体板冷压成形的残余应力研究的综述报告引言:船体板冷压成形技术是一种比较新颖的成形技术,它是指利用机械力和液压原理,在常温下通过特殊工艺方法对船体板材进行成形。相比于传统的热成形技术,冷压成形技术具有许多优点,如产品精度高、成形速度快、能耗低等。但是,船体板冷压成形技术的一个不容忽视的问题就是残余应力。本文对船体板冷压成形中残余应力的研究进行综述。研究内容:1.船体板冷压成形原理以及残余应力的产生机理船体板冷压成形技术是利用特殊的成形模具和压力,对中厚板进行成形。成形时,板材经过模具之后,会受到极大的塑性
三维曲面船体外板板材成形国内外研究现状.docx
三维曲面船体外板板材成形国内外研究现状
船体曲面焊接装置.pdf
本发明涉及焊接加工领域,具体公开了一种船体曲面焊接装置,整个装置能让焊接装置沿着船体和被焊接件的焊接处平稳的移动,对焊接处进行均匀的焊接,实现了船体曲面自动化的焊接;且焊接的过程中充分的利用了气泵产生的动能,一方面带动滑轮和伸缩杆移动,另一方面对伸缩杆的伸缩进行控制。本方案可以高效的将被焊接件与曲面的船体进行焊接。
船体曲面焊接方法.pdf
本专利涉及焊接加工领域,具体公开了一种船体曲面焊接方法,方法中使用了一种焊接装置,该焊接装置能够通过调节气泵的排气量来控制叶轮转动,转动的叶轮带动第一转杆、主动带轮、从动带轮和第二转杆转动,然后第二带轮带动槽轮在导槽内速度,实现了动力的转化和传动;气泵排出的气体可让圆柱体杆会发生相对移动,进而实现伸缩杆的伸缩长度的控制;在焊接的过程中,滚轮上的设置的压力传感器还能反馈滚轮受到的压力,再通过处理器处理信号,处理器对气泵的排气量进行控制,进而让滚轮受到的压力保持稳定,使焊接装置的焊接过程保持稳定。本方案能对曲