
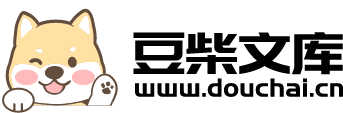
一种高耐久性轮辐辐底的设计方法.pdf
文宣****66
亲,该文档总共11页,到这已经超出免费预览范围,如果喜欢就直接下载吧~
相关资料
一种高耐久性轮辐辐底的设计方法.pdf
本发明涉及汽车及机械工程技术领域,尤其涉及一种高耐久性轮辐辐底的设计方法。本发明通过对轮辐辐底独特的设计方法,能够大幅度提升辐底耐久性能,使得失效点不会像现有设计方法那样出现在轮辐辐底,避开设计瓶颈,进一步通过对回转体曲线优化达到轻量化目的。
一种车轮轮辐的辐底平面度测量装置.pdf
本发明公开了一种车轮轮辐的辐底平面度测量装置,包括:测量本体,以及位于所述测量本体上的测量机构;所述测量本体为与车轮轮辐的辐底内外表面相适的环状结构,所述测量本体的下表面能够与所述辐底内表面或外表面相接触,并能够沿所述辐底内表面或外表面的周向转动或径向移动;所述测量机构包括:固定座,以及通过所述固定座安装于所述测量本体上的测量仪;所述固定座安装于所述测量本体的外表面;所述测量仪的测量杆能够穿过所述固定座,经所述固定座固定于所述测量本体上,且位于所述测量杆端部的测量触头与所述辐底的内表面或外表面相抵接,并随
用于辐板式车轮的车轮辐板.pdf
本发明提出了一种用于辐板式车轮的车轮辐板,所述辐板式车轮尤其用于多用途车辆,所述车轮辐板具有基本上径向延伸的轮毂装配凸缘(11)和可以接合到轮辋的基本上柱状辐板边缘(13),并且所述车轮辐板具有在所述轮毂装配凸缘(11)和所述辐板边缘(13)之间延伸的过渡区(14),其中,所述过渡区被细分为进入彼此或者进入所述轮毂装配凸缘(11)或所述辐板边缘(13)的至少五个片段(A
一种高耐久性机制砂混凝土配合比的设计方法.pdf
本发明提供了一种高耐久性机制砂混凝土配合比的设计方法,属于建筑材料技术领域。该高耐久性机制砂混凝土配合比的设计方法,根据富勒曲线最大密实度理论,将机制砂和粗集料作为堆积体系,通过考虑机制砂石粉含量、粗集料空隙率、砂浆厚度等因素,从设计方面解决了现有机制砂混凝土配合比设计方法因忽略集料级配比例而出现的密实度,以及耐久性设计不合理的问题,为高耐久性机制砂混凝土的配合比设计提供了一种新方法。
一种高耐久性岩棉及其制备方法.pdf
本发明涉及岩棉技术领域,具体为一种高耐久性岩棉及其制备方法,包括岩棉组分和改性溶胶溶液,岩棉组件包括以下重量份原料:玄武岩300‑400份、白云石100‑200份、高炉矿渣100‑120份、焦炭80‑100份;本发明通过在岩棉组分表面形成凝胶,最终实现岩棉组分表面附着有二氧化硅气凝胶,降低了岩棉组分的导热率,提高了岩棉产品的绝热性;由于二氧化硅气凝胶表面具有亲水基,容易让岩棉组分吸湿而增大了导热率,降低保温效果,本发明再利用甲醇蒸汽进行氧化处理,醇羟基与凝胶表面的硅羟基发生脱水缩合反应,使得硅羟基转变为S