
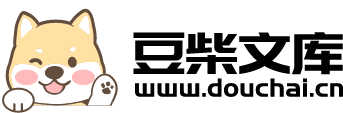
异形金属件的锻造工艺.pdf
秀华****魔王
在线预览结束,喜欢就下载吧,查找使用更方便
相关资料
异形金属件的锻造工艺.pdf
本发明提供了一种异形金属件的锻造工艺,包括如下步骤:A、通过异形挤压模具挤压出异形截面的棒料;B、从棒料上切割出一定厚度的片料;C、对片料进行精锻、切飞边及热处理完成锻造;所述的步骤A中棒料的截面与最终产品的锻造所需的胚料的轮廓一致,步骤B中片料的厚度与最终产品的锻造所需胚料的厚度一致。上述方案中将现有技术中的异形锻造件的前四个工艺步骤(下料、墩粗、预成型、粗锻),整合成一个型材挤出成型工艺和一个简单的下料切片工艺,大大的缩短了工艺路线并降低了异形锻造件开发的成本。
一种异形沟道钟形壳的锻造工艺.pdf
本发明提出了一种异形沟道钟形壳的锻造工艺,其包括:下料,选择合适直径和段长的坯料;制坯,去除坯料表面氧化皮,将坯料的重量控制到合理范围内以获得合格的毛坯;温锻正挤,对毛坯的一端进行温锻正挤以实现杆部的成形;温锻镦粗,对毛坯的另一端进行温锻镦粗以实现壳部的外部轮廓的成型;温锻成形,使用温锻成形模具对毛坯进行温锻以实现壳部、过渡部的初步成形从而获得钟形壳初成品,所述钟形壳初成品的壳部的内壁上额外形成有若干退料筋,所述钟形壳初成品的壳部的外壁上额外形成有波浪状的起伏结构;冷锻成形,使用冷锻成形模具对钟形壳初成品
一种异形锻造件的锻造装置.pdf
本发明公开了一种异形锻造件的锻造装置,包括支撑架,所述支撑架的底部安装有底框,所述底框的内部设置有用于对加工件本体底部进行支撑的支架组件,所述支撑架的顶部通过水平驱动组件连接有用于对加工件本体进行加工的锻造机构,所述锻造机构包括连接架,所述连接架上固定有安装架,所述安装架的相对面分别滑动安装有活动块,所述安装架的内壁设置有两组连杆机构,所述连杆机构可用于活动块和活动柱的分级滑动。本发明解决了异形件锻造过程的难以夹持的问题,提高了工作效率,利用活动柱与活动块的速率不同,分别作用于加工件本体的锻造和夹紧,在保
一种异形金属件的固定夹具.pdf
本实用新型提供一种异形金属件的固定夹具,应用在工装夹具技术领域,其技术方案要点是:包括固定主板,固定主板上固定设置有固定板,位于固定板的一侧的固定主板上固定设置有调节块,调节块上滑移连接有调节板,调节板与固定板之间形成用于容纳异形金属件主体的固定槽;调节板与固定主板之间设置有通过调整调节板在调节块上滑移来调节固定槽的槽宽的调节件;具有的技术效果是:固定夹具结构简单,易操作,节省生产成本,提高工作人员的工作效率;并且能够牢固地将异形金属件固定,保证生产品质。
含有耳部的异形封头锻造方法.pdf
本发明提供了一种含有耳部的异形封头锻造方法,包括如下步骤:先将封头坯料锻造成规则环状;将规则环状的封头坯料在始锻温度下加热、保温,出炉后将封头坯料对中放入下模,导向柱插入封头坯料中孔;下模上设有与封头锻件形状对应的通孔、型腔、台阶形环腔,通孔内置有垫环,导向柱与垫环配合;将上模下压,使封头坯料外侧与垫环上端至型腔之间的壁面贴合,封头主体部分的厚度压到封头锻件所需厚度,成形封头底部;将成形压环对中套在上模上,成形压环下压进入台阶形环腔,直至台阶形环腔填充满,制得带耳异形封头锻件。采用本发明,使得带耳异形封头