
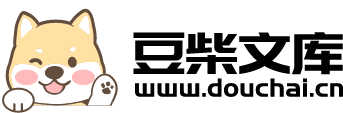
一种重型燃机涡轮叶片气膜孔位置度确定方法.pdf
波峻****99
在线预览结束,喜欢就下载吧,查找使用更方便
相关资料
一种重型燃机涡轮叶片气膜孔位置度确定方法.pdf
本发明涉及机械特种加工领域,具体是一种重型燃机涡轮叶片气膜孔位置度确定方法,包括以下步骤:S01:建立重型燃机涡轮叶片三维模型;S02:将待加工重型燃机涡轮叶片放置在三坐标测量机工作台上,将重型燃机涡轮叶片三维模型导入三坐标软件自动找正并建立坐标系;S03:利用三维模型的原始理论数据,结合设计文件的技术要求进行编程,确定三维空间气膜孔的位置;S04:在三坐标测量机的测针上涂上颜料,运行编好的三坐标点位程序,三坐标测量机的测针在叶片型面上留下颜料的印记,确定三维空间气膜孔的位置。本发明提高了气膜孔的加工效率
一种重型燃机涡轮叶片热障涂层的制备方法.pdf
本发明涉及一种涂层的制备方法,具体涉及一种重型燃机涡轮叶片热障涂层的制备方法。本发明包括如下步骤:一、利用EB-PVD技术在重型燃机涡轮叶片上制备CoCrAlY粘结层,对所述CoCrAlY粘结层进行真空扩散处理;二、对CoCrAlY粘结层的表面,使用通用喷丸设备,应用玻璃丸进行喷丸处理;三、对带有CoCrAlY粘结层的重型燃机涡轮叶片进行消除应力热处理;四、利用EB-PVD技术在带有CoCrAlY粘结层的重型燃机涡轮叶片上制备YSZ面层。本发明的重型燃机涡轮叶片热障涂层的制备方法,解决重型燃机涡轮叶片表面
用于涡轮叶片气膜孔的检测方法.pdf
一种用于涡轮叶片气膜孔的检测方法,包括:将树脂涂在涡轮叶片表面及气膜孔内表面;对树脂进行固化,使得固化后的树脂贴合涡轮叶片表面及气膜孔内表面,形成与涡轮叶片结构相同的树脂固化体;将树脂固化体分割成多块,并从涡轮叶片上取下;分别测量分割后的每块树脂固化体的几何形貌;将每块树脂固化体的几何形貌进行拼接,获得涡轮叶片及气膜孔的整体结构模型,根据整体结构模型得到气膜孔相对于涡轮叶片表面的结构、位置及角度。该方法保留了气膜孔结构与叶片的相对位置特征,能够便于全面、系统检测气膜孔的结构形式及精度,且光固化效率高,能够
一种涡轮叶片气膜孔精密成形方法.pdf
本发明公开了一种涡轮叶片气膜孔精密成形方法,属于基于光固化成型技术快速铸造领域。包括:1)用光固化快速成型技术制造涡轮叶片树脂模具;2)通过凝胶注模法向涡轮叶片的树脂模具原型中浇注陶瓷浆料得到铸型坯体,实现气膜孔陶瓷芯的成型;3)真空冷冻干燥和高温烧结对气膜孔陶瓷芯进一步强化,实现不同陶瓷基气膜孔陶瓷芯的成型;4)针对不同类型陶瓷基的气膜孔陶瓷芯,结合定向凝固技术,可实现多种高温合金的气膜孔铸造成型,最后通过脱芯工艺去除残留在金属叶片及气膜孔内的陶瓷芯,实现铸造气膜孔高质量成型。本发明设计合理,操作简便,
一种精准加工涡轮叶片气膜孔的方法.pdf
本发明涉及一种精准加工涡轮叶片气膜孔的方法,属于激光应用领域。本发明的目的是为了解决传统飞秒激光在涡轮叶片制孔过程中孔口圆度低、孔内壁粗糙度高、孔内壁不均匀等一些列技术问题。本发明首次采用垂直偏振的飞秒激光双脉冲序列加工微孔,并应用于涡轮叶片气膜孔的制备,制备出高质量高精度微孔,有效地提高气膜冷却孔的孔口圆度以及孔壁的均匀性。