
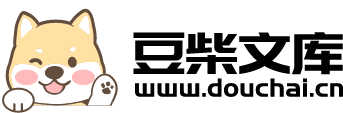
用于涡轮叶片气膜孔的检测方法.pdf
霞英****娘子
在线预览结束,喜欢就下载吧,查找使用更方便
相关资料
用于涡轮叶片气膜孔的检测方法.pdf
一种用于涡轮叶片气膜孔的检测方法,包括:将树脂涂在涡轮叶片表面及气膜孔内表面;对树脂进行固化,使得固化后的树脂贴合涡轮叶片表面及气膜孔内表面,形成与涡轮叶片结构相同的树脂固化体;将树脂固化体分割成多块,并从涡轮叶片上取下;分别测量分割后的每块树脂固化体的几何形貌;将每块树脂固化体的几何形貌进行拼接,获得涡轮叶片及气膜孔的整体结构模型,根据整体结构模型得到气膜孔相对于涡轮叶片表面的结构、位置及角度。该方法保留了气膜孔结构与叶片的相对位置特征,能够便于全面、系统检测气膜孔的结构形式及精度,且光固化效率高,能够
涡轮叶片的气膜孔结构.pdf
本发明的涡轮叶片的气膜孔结构,属于涡轮叶片的技术领域,解决现有技术中叶片上气膜孔的气膜覆盖率较低,降低叶片的冷却效果的技术问题。所述气膜孔结构包括在气流方向上以一体式的方式依次设置的圆柱段、凸起段、收缩段、扩张段和出口面,以适用于涡轮叶片的外部冷却,提高涡轮叶片冷气覆盖效果。
涡轮叶片的V型气膜孔和涡轮叶片.pdf
本发明公开了一种涡轮叶片的V型气膜孔和涡轮叶片,涡轮叶片的V型气膜孔包括冷气入口、冷气出口,V型气膜孔相对于空间坐标系具有空间倾斜角度的倾斜主圆柱孔,倾斜主圆柱孔的一端连通至冷气入口,另一端连通至冷气出口;V型气膜孔还包括由冷气出口处向冷气入口方向开设的倾斜副圆柱孔,冷气出口沿展向扩张以构成倾斜副圆柱孔的副冷气出口;倾斜副圆柱孔与倾斜主圆柱孔之间呈夹角布设,倾斜主圆柱孔和倾斜副圆柱孔组合构成V型孔结构。本发明的涡轮叶片的V型气膜孔,在倾斜主圆柱孔基础上,引入倾斜副圆柱孔形成V型孔结构,二者都具有空间角,即
涡轮叶片气膜孔孔周的应变测量方法.pdf
本公开涉及涡轮叶片技术领域,尤其涉及一种涡轮叶片气膜孔孔周的应变测量方法。该应变测量方法包括:提供一涡轮叶片的试验件,该试验件上设有多个气膜孔;在试验件的表面上制作散斑,并使散斑区域覆盖各个气膜孔;根据试验件的表面尺寸和受载后的变形量,预估出试验件的视野范围;将采集相机安装在支撑架上,并结合预估出的视野范围对采集相机进行调整;对具有散斑的试验件进行拉伸试验,并利用采集相机采集试验件在拉伸过程中的散斑图像;对采集相机采集到的散斑图像进行后期处理,以得到气膜孔孔周的应变数据。该应变测量方法能够实现气膜孔的非接
高压涡轮工作叶片冷却气膜孔检测平台及测试方法.pdf
本发明公开了一种高压涡轮工作叶片冷却气膜孔检测平台及测试方法,包括气体加热装置、冷却系统、工件调节系统、支撑机架、控制系统、热成像仪、显示单元、工作气源、压缩空气气源、热气测温传感器、第一角阀座、第二角阀座、工件测温传感器和浮子流量计;浮子流量计的输入端与工作气源连接,浮子流量计的输出端与气体加热装置的输入端连接,气体加热装置的输出端与工件调节系统相连接,在气体加热装置和工件调节系统之间的管路中设有第一角阀座和热气测温传感器;冷却系统与气体加热装置采用并联方式连接工件调节系统,在冷却系统与工件调节系统之间