
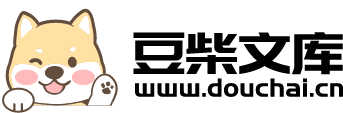
离合助力器CAE分析报告.doc
yy****24
在线预览结束,喜欢就下载吧,查找使用更方便
相关资料
离合助力器CAE分析报告.doc
离合助力器支架CAE分析张敏北汽福田汽车股份有限公司长沙汽车厂技术中心CAE分析室长沙410129一、分析方法1、建模方法:离合助力器支架采用6面体单元建模,螺栓连接采用beam单元模拟。2、材料属性:材料名称牌号弹性量(MPa)泊松比密度(Kg/mm3)抗拉强度(MPa)延伸率铸铝ZL1117.7e40.332.7e-62053%3、边界条件:离合助力器支架受载如表6-2所示;表6-2离合助力器支架受载情况名称载荷(N)×冲击系数约束离合助力器支架3000×1.3≈4000连接螺孔处4、加载曲线如图6-
离合器助力器项目评估分析报告.docx
离合器助力器项目评估分析报告离合器助力器项目评估分析报告目录TOC\h\zHYPERLINK\l_Toc18617前言PAGEREF_Toc18617\h3HYPERLINK\l_Toc32325一、技术方案与建筑物规划PAGEREF_Toc32325\h3HYPERLINK\l_Toc12499(一)、设计原则与离合器助力器项目工程概述PAGEREF_Toc12499\h3HYPERLINK\l_Toc29188(二)、建设选项PAGERE
离合器助力器.pdf
一种离合器助力器,包括外壳、液腔、气腔、在液压和气压的作用下向前推动助力推杆的助力活塞以及在液压的作用下向所述气腔进气以从助力活塞活塞盘后侧面向前推动该助力活塞的进气阀,所述液腔内具有油封以及第一气封,所述助力活塞为塑料活塞,所述油封以及第一气封轴向由后至前固定于所述活塞杆的后端。本发明由于在活塞杆的后端使用了动密封,离合器摩擦片磨损后,助力活塞的前后支撑点的距离不变,不会因为结构失稳而造成油封和气封受挤压不均,影响密封效果,同时,采用塑料活塞重量轻,更加不容易造成油封和气封受挤压不均。
基于CAE分析的上离合器注射模设计.docx
基于CAE分析的上离合器注射模设计摘要:本文旨在探讨基于CAE分析的上离合器注射模设计的优化方法。在汽车制造过程中,离合器的性能和使用寿命对车辆的整体质量至关重要。为了提高离合器的使用寿命和性能,需要对上离合器注射模进行优化设计。在本文中,我们通过CAE分析技术对注射模进行优化设计,以获得更好的性能和寿命。我们的研究结果表明,基于CAE分析的上离合器注射模设计可以显著提高离合器的性能和使用寿命。关键词:CAE分析,上离合器,注射模设计,性能,使用寿命1.引言汽车离合器是汽车传动系统中一个非常重要的零部件,
一种离合助力器制备工艺.pdf
本发明公开了一种离合助力器制备工艺,其技术要点是:包括以下步骤:S1、铸坯:在1390‑1430℃的中频感应电炉进行熔炼,并铸造坯料;S2、锻造:将锻造的坯料在500‑600℃下进行模锻,得到离合器盘主体;S3、初定型:采用立钻内拱的方式进行初定型;S4、热处理;S5、镗孔;S6、车端面;S7、车倒角:旋转刀架的角度,使车刀刃与工件轴心线形成一定的角度,然后按图纸要求的倒角大小进刀;S8、涂装;本离合助力器制备工艺能够节省加工材料,加工的更加精准,且对离合器助力器主体采用了淬火、回火等工艺能够生产出强度和