
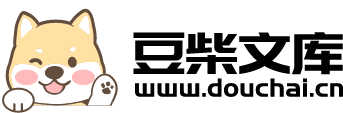
设备管理与TPM实战训练.ppt
kp****93
亲,该文档总共111页,到这已经超出免费预览范围,如果喜欢就直接下载吧~
相关资料
设备管理与TPM实战训练.ppt
设备管理与TPM实战训练第一讲设备管理之基础部分1.设备管理目的:计算方法请计算MTBF和MTTR:9月11日设备总运转时间:8小时(8:00~12:00,13:30~17:30)设备发生故障记录如下:9:10故障,通知维修,9:20分正常;10:00故障,15分钟后修复;14:00故障,14:05找到维修员,14:15分修复;15:30故障,停止了5分钟。三好四会制五项纪律结论:要想生产更加顺畅,制造和保全之间协调非常重要。为此制造部门不仅仅管生产还要分担部分保全,而保全部门也要负有生产责任。设备三级保
全员设备管理与维护实战训练(TPM).ppt
浙江吉鑫祥叉车制造有限公司ZhejiangGoodsenseforkliftCo.,LTD丰田等企业为什么会成功1.追求精细化管理,维护管理工具丰田公司数十年如一日的不断追求精细化管理,追求零库存、零缺陷、低成本和零损耗等。丰田公司有效地运用了各种各样的管理工具,如5S体验活动,TQC、TPM、IE、JIT等,为企业的管理提升服务。这些管理工具在丰田都能得到有效的坚持,这是它获得成功的必要条件之一。2.注重人才的培养丰田公司注重人才的培育,也是它成功的重要方面。它提倡的企业使命是“造物、育人”,经营理念则
设备管理实战与TPM.ppt
全员生产设备管理(PTM)企业、生产、设备、效率、人员关系设备管理的内容设备综合管理六阶段配置合理使用合理保养合理维修合理改造合理更换合理定位和点检的适应性设备管理目的是:让设备保持良好的效率状态设备2中国“特色”的设备管理事后保全BM一、生产操作使用的记录跟踪二、设备上与生产相关的工艺参数记录跟踪三、设备主要功能参数记录跟踪四、设备使用守则:1、持证上岗操作设备2、交接班管理制度3、按操作规程及“四项要求”使用设备4、“三好”、“四会”、“五项纪律”设备管理制度:1、设备操作证上岗制度
设备管理及TPM实战.doc
2011新版课程.精选范本李铁华实战课程JY-2011-01课程属性【精益设备管理类】2011新版课程设备管理及TPM实战背景:本课程根据客户需求定制开发范围:适用于企业设备管理精益及开展有效的TPM活动设计思路:根据客户培训需求调查,根据客户受众特点,结合8年日企工作经历及10年咨询经验,主要讲透以下三个内容:、概念厘清:TPM是什么?TPM与设备管理及5S的关系?TPM包括哪些内容?业务实操—根据需求需求界定为2个主要内容:1自主保全---涉及现场设备点检的分工,点检部位,点检频次及OPL方法等,主要
全员设备管理与维护实战训练(TPM)(PPT107页).ppt
浙江吉鑫祥叉车制造有限公司ZhejiangGoodsenseforkliftCo.,LTD丰田等企业为什么会成功1.追求精细化管理,维护管理工具丰田公司数十年如一日的不断追求精细化管理,追求零库存、零缺陷、低成本和零损耗等。丰田公司有效地运用了各种各样的管理工具,如5S体验活动,TQC、TPM、IE、JIT等,为企业的管理提升服务。这些管理工具在丰田都能得到有效的坚持,这是它获得成功的必要条件之一。2.注重人才的培养丰田公司注重人才的培育,也是它成功的重要方面。它提倡的企业使命是“造物、育人”,经营理念则