
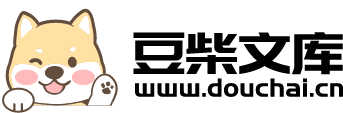
克服成形缺陷对策和改善高强钢板成形性技术.pdf
as****16
在线预览结束,喜欢就下载吧,查找使用更方便
相关资料
克服成形缺陷对策和改善高强钢板成形性技术.pdf
克服成形缺陷对策和改善高强钢板成形性技术TohruYoshida1,KoichiSato2,EijiIsogai3,JunNitta1,HiroshiYoshida1(1.钢铁研究实验室,新日铁与住友金属公司,20-1新富,富津市,千叶市,日本;2.名古屋研发实验室,新日铁与住友金属公司,5-3东海町,东海,爱知,日本;3.广畑R&D实验室,新日铁与住友金属公司,1富士町,广畑区,姬路,兵库县,日本)摘要:把高强钢板用于汽车车身零部件,回弹是最难解决的问题之一。通过现象分类回弹的行为机制并且报告了基于每个
用于制造具有改善的延展性和可成形性的高强度钢板的方法和所获得的钢板.pdf
一种用于制造钢板的方法,所述方法包括以下顺序步骤:‑提供冷轧钢板,所述钢的化学组成以重量%计包含:0.15%≤C≤0.23%,1.4%≤Mn≤2.6%,0.6%≤Si≤1.5%,0.02%≤Al≤.0%,其中1.0%≤Si+Al≤2.0%,0≤Nb≤0.035%,0≤Mo≤0.3%,0≤Cr≤0.3%,剩余部分为Fe和不可避免的杂质;‑将所述钢板在Ac1至Ac3的退火温度TA下退火以获得包含至少40%的奥氏体和至少40%的亚温铁素体的组织;‑使所述板以至少20℃/秒的冷却速率从至少600℃的温度淬火至18
具有高强度和高成形性的钢板及其制造方法.pdf
根据本发明的一个方面的具有高强度和高成形性的钢板包含(以重量%计):0.12%至0.22%的碳(C);1.6%至2.4%的硅(Si);2.0%至3.0%的锰(Mn);0.01%至0.05%的铝(Al);总量大于0且小于或等于0.05%的在钛(Ti)、铌(Nb)和钒(V)中的一种或多种;0.015%或更少的磷(P);0.003%或更少的硫(S);0.006%或更少的氮(N);以及余量的铁(Fe)和其它不可避免的杂质,所述钢板具有850MPa或更大的屈服强度(YS)、1180MPa或更大的抗拉强度(TS)、1
用于制造具有改善的可成形性的高强度钢板的方法及所获得的板.pdf
一种用于制造具有改善的可成形性偏析的高强度板的方法,根据该方法,钢的化学组成以重量百分比计包含:0.1%≤C≤0.4%;4.2%≤Mn≤8.0%;1%≤Si≤3%;0.2%≤Mo≤0.5%;剩余部分为Fe和不可避免的杂质,该方法包括以下步骤:通过在高于钢的Ac3转变点的退火温度AT下对由所述钢制成的轧制板进行均热处理,以对该轧制板进行退火;通过将该板冷却至在Ms转变点与Mf转变点之间的淬火温度QT,对该板进行淬火,以获得包含至少65%的马氏体和至少20%的残余奥氏体,铁素体含量加贝氏体含量之和小于10%的
用于生产具有改善的强度和可成形性的高强度钢板的方法以及所获得的高强度钢板.pdf
用于生产具有以下显微组织的钢板的方法:所述显微组织由总和为71%至91%的马氏体和贝氏体、9%至13%的残留奥氏体以及至多20%的铁素体组成,所述方法包括:‑提供冷轧钢板,所述钢的化学组成以重量%计包含:0.13%≤C≤0.22%.2%≤Si≤2.3%0.02%≤Al≤1.0%,其中1.25%≤Si+Al≤2.35%,2.4%≤Mn≤3%,Ti