
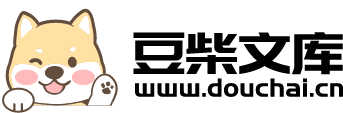
一种可折叠和翻转的盖板及其制备工艺.pdf
宛菡****魔王
在线预览结束,喜欢就下载吧,查找使用更方便
相关资料
一种可折叠和翻转的盖板及其制备工艺.pdf
本发明公开了一种可折叠和翻转的盖板及其制备工艺,属于汽车内饰技术领域。本发明的可折叠和翻转的盖板包括第一面板、第二面板和连接面料;所述第一面板的一侧边界设置有第一台阶面,所述的第二面板的一侧边界设置有与第一台阶面相互配合的第二台阶面,所述的第一面板与第二面板通过第一台阶面和第二台阶面相互搭接;所述的连接面料与第一面板和第二面板的一侧表面连接。本发明的可折叠和翻转的盖板,通过增加一个台阶封边,解决了产品成型过程中的工艺问题,减少了露玻纤和分层。在产品装配后这个台阶也可以反向相互支撑,有效的杜绝了承载时凹入掉
一种盖板玻璃组件及其制备工艺.pdf
本发明公开了一种盖板玻璃组件及其制备工艺,旨在提供一种组装方便、容易拆装、结构稳定和生产效率高的盖板玻璃组件及其制备工艺。包括面板和盖板玻璃本体,面板上设有放置槽,盖板玻璃本体安装在放置槽内,盖板玻璃本体的上表面边缘处为弧形状,放置槽内设有连接件,盖板玻璃本体通过连接件与面板连接。本发明的有益效果是:盖板玻璃组件可实现快速的组装、拆卸,结构配合流畅、连接强度高,结构稳定、使用寿命长,缩短了盖板玻璃的制作工艺步骤,降低了加工时长、提高了加工效率,产品美观线条流畅,达到提高整个生产的效率和产品可观性的效果。
一种可折叠眼镜框架及其制备工艺.pdf
本发明属于眼镜框架领域,具体的说是一种可折叠眼镜框架及其制备工艺,包括镜圈,镜圈之间设置有鼻梁,鼻梁包括铰接杆一与铰接杆二,铰接杆一与铰接杆二相互铰接,铰接杆一与铰接杆二远离铰接点的一端均与相对应的镜圈的侧壁固定连接;两个镜圈远离鼻梁的一侧均固定安装有桩头;镜腿包括第一连接杆与第二连接杆,第一连接杆靠近镜圈的一端与桩头远离镜圈的一端相铰接,第一连接杆远离桩头的一端铰接有第二连接杆;第二连接杆远离第一连接杆的一端固定安装有脚套;套筒包括第一套管与第二套管,第一套管的内圈与第二套管的外圈滑动连接;本发明结构简
一种陶瓷盖板制备工艺.pdf
本发明公开了一种陶瓷盖板制备工艺,包括以下步骤:称重:按配比分别称取固体原料;球磨:将固体原料混合均匀后进行球磨;混料:将球磨后的混合粉料与有机溶剂按重量比为1:1‑3的配比混合成浆料;成型:将浆料分别注射到陶瓷盖板模具和陶瓷基座模具中成型,得到陶瓷盖板坯体和陶瓷基座坯体;装配:在陶瓷基座坯体上覆盖一层隔粘粉后,再装配陶瓷盖板坯体与陶瓷基座坯体;烧结:将装配好的陶瓷盖板坯体与陶瓷基座坯体一同放入烧结炉中,在1300‑1600℃中烧结5‑20小时,得到陶瓷盖板和陶瓷基座;对陶瓷盖板去毛刺,得到产品。采用本发
一种陶瓷盖板制备工艺.pdf
本发明提供了一种陶瓷盖板制备工艺,包括如下步骤:装配;冷等静压;脱模;第一次烧结,将装有所述预烧坯体的坩埚置于烧结炉内进行烧结,烧结温度850‑900℃,升温速度5~8℃/min,保温8‑9h,得第一陶瓷坯体;加工,对第一陶瓷坯体进行机械加工控制尺寸精度,得第二陶瓷坯体;第二次烧结,将装有第二陶瓷坯体的坩埚置于烧结炉内,烧结温度1200‑1350℃,升温速度5~8℃/min,保温8‑9h,得所述陶瓷盖板成品。所述陶瓷盖板制备工艺采用二次烧结工艺,可使用常规的加工设备对陶瓷坯体进行加工,以得净尺寸的陶瓷盖板