
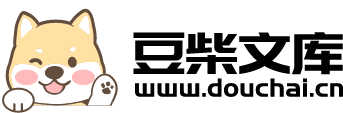
超厚铜板的孔加工方法.pdf
曦晨****22
亲,该文档总共11页,到这已经超出免费预览范围,如果喜欢就直接下载吧~
相关资料
超厚铜板的孔加工方法.pdf
本申请提供一种超厚铜板的孔加工方法。上述的超厚铜板的孔加工方法包括如下步骤:获取多个超厚铜板;对每一超厚铜板进行蚀刻操作,以使每一超厚铜板上蚀刻形成蚀刻孔,其中,每一超厚铜板的蚀刻孔处于通孔区域内,且多个超厚铜板的蚀刻孔对应设置;将多个超厚铜板进行压合操作,得到多层线路板;对多层线路板进行钻孔操作,以钻除通孔区域形成通孔。上述的超厚铜板的孔加工方法钻孔效率较高,加工时不易短钻咀,且能较好地提高钻咀使用寿命和提高线路板的品质。
厚铜板封孔方法及厚铜板制作方法.pdf
本申请提供一种厚铜板封孔方法及厚铜板制作方法。上述的厚铜板封孔方法,包括:对厚铜板进行钻孔操作,以使厚铜板形成圆孔;对圆孔的内壁进行金属化处理;将干膜压合于厚铜板,干膜覆盖于圆孔,干膜的厚度为50微米,以形成干膜板;对干膜板进行曝光处理,曝光尺七格,曝光时静置干膜板30分钟以上,以在干膜上曝出所需的线路,进而形成曝光板;对曝光板进行显影操作,以将未发生聚合反应的干膜冲掉,以形成显影板;对显影板进行蚀刻操作,以蚀刻掉显影后露出的铜面,以形成蚀刻板;对蚀刻板进行退膜操作。由于干膜的厚度为50微米,避免了厚铜板
一种改善阻焊厚铜板塞孔不良的加工方法.pdf
本发明公开了一种改善阻焊厚铜板塞孔不良的加工方法,包括:步骤S1,前工段来料通过阻焊前处理;步骤S2,进行阻焊前塞孔;步骤S3,第一次阻焊时印刷厚铜板两面面油;步骤S4,预烤,将湿润面油初步固化;步骤S5,第一次曝光,使用LMS菲林+曝孔菲林技术;步骤S6,进行第一次显影;步骤S7,采用分段固化烘烤;步骤S8,烘烤后的厚铜板进行前处理;步骤S9,第二次阻焊时印刷厚铜板两面面油;步骤S10,第二次曝光,使用菲林技术;步骤S11,进行第二次显影;步骤S12,高温烘烤。本发明有效的避免了常规操作流程中在塞孔前0
多层盲埋孔导热厚铜板生产方法.pdf
本发明提供了一种多层盲埋孔导热厚铜板生产方法,包括:所述多层盲埋孔导热厚铜板在压合前,向导热材料中添加氧化铝、氧化镁、氮化物等导热填充物,板对位方式采用手动PINLAM系统,对位精度小于0.025mm;对位用的孔采用钻出以减少打靶导致的误差;正式压合前先抽真空3‑5分钟,真空度达到680mmhg后启动热压;每次压合完,用三次元测量其涨缩,根据其涨缩重新绘线路菲林及钻带,以确保钻孔与图形的对准度。本发明可利用生产FR4的厚铜多层板工艺来生产导热厚铜盲埋孔板,对一些工序的工艺参数进行优化,以达到客户要求,特
高层盲埋孔厚铜板制作探讨.docx
高层盲埋孔厚铜板制作探讨一、引言高层建筑物的电路系统是一个非常重要的系统。它必须能够保证设备的正常运行和安全性。铜板作为电路系统中的主要材料之一,其视觉效果和传导性能受到了广泛的关注。在铜板的制作中,高层盲埋孔厚铜板制作技术是一种非常重要的技术,它可以提高铜板的覆盖面积,同时提高了铜板的传导性能和视觉效果。二、高层盲埋孔厚铜板制作的步骤1.设计铜板的厚度和覆盖面积。根据电路系统的要求和技术参数,确定铜板的厚度和面积。2.制作铜板模板。根据设计要求制作铜板的模板,模板应具有高度精度和可重复性。3.铜片制备。