
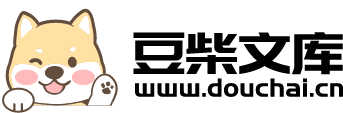
一种减少渣量的转炉炼钢法.pdf
书生****ma
亲,该文档总共13页,到这已经超出免费预览范围,如果喜欢就直接下载吧~
相关资料
一种减少渣量的转炉炼钢法.pdf
本发明属于转炉炼钢技术领域,提供了一种减少渣量的转炉炼钢法,该工艺流程为循环工艺过程,起点定为溅渣护炉,终点为炉内留渣;由溅渣护炉、炉内液态渣固化、添加废钢、兑入铁水、第一阶段吹炼-脱磷阶段、中间倒渣、第二阶段吹炼-脱碳阶段、出钢和炉内留渣八个阶段组成,对比常规转炉炼钢工艺,在终点磷含量不大于0.015%前提下,石灰消耗降低了40.5%,轻烧白云石消耗降低了76.8%,二者总消耗降低了55.5%。
小渣量转炉炼钢方法.pdf
本发明涉及一种小渣量转炉炼钢方法,该方法是按以下步骤进行:a、上炉出钢后保留80%以上的炉渣;b、倾炉,加废钢、兑铁水,摇正炉体;c、降枪供氧,开始吹炼;d、待硅锰氧化结束时起枪倒渣;e、按普通渣料加入总量的48-54%,加料造渣并继续吹炼;f、当吹炼达到终点成分范围时,停止供氧,倒炉取样并测温,快速分析碳、硫和磷含量;g、当成分和温度符合规定要求时,倒炉出钢;h、出钢时进行脱氧合金化处理,同时保留80-100%的炉渣量,准备下一炉钢的吹炼。本发明通过改变传统炼钢造渣工艺,在不增加设备、不增加原料成本和不
减少渣量的转炉工艺研究与实践.docx
减少渣量的转炉工艺研究与实践标题:减少渣量的转炉工艺研究与实践摘要:钢铁行业是全球资源消耗量较大的行业之一,同时也是重要的能源消耗行业。在钢铁生产过程中,转炉炼钢是一种常用的工艺,它对于提高炼钢效率和降低成本起到重要作用。然而,转炉炼钢过程中产生的渣量较大,给环境和资源带来了一定的压力。本文在对转炉炼钢工艺原理进行分析的基础上,结合实际情况研究了减少渣量的转炉工艺,并通过实践验证了该工艺的可行性和效果。最后,提出了进一步改进和优化的建议。关键词:转炉炼钢;渣量;环境保护;资源利用;工艺改进一、引言转炉是炼
一种降低转炉冶炼钢渣渣量的工艺.pdf
本申请提出了一种降低转炉冶炼钢渣渣量的工艺,涉及炼钢技术领域。一种降低转炉冶炼钢渣渣量的工艺,包括如下步骤:将上一炉的脱碳炉渣留在转炉内,再加入造渣剂,溅渣护炉;向炉内加入废钢和铁水,进行一次冶炼5‑9min;对一次冶炼后的炉体进行排渣处理,获得一次处理钢液;向排渣处理后的炉内加入轻烧白云石,再将炉体内的一次处理钢液进行二次冶炼8‑12min,分离出炼钢液和脱碳炉渣。通过进行两次排渣,对一次冶炼后的炉体进行排渣处理,可将氧化后的磷随着炉渣排出,降低了一次处理钢液中的磷含量,在二次排渣时脱碳,避免碳和氧化铁
一种降低转炉冶炼钢渣渣量的工艺.pdf
本发明公开一种降低转炉冶炼钢渣渣量的工艺,工艺包括:炼钢工艺采用100t顶底复吹转炉冶炼,由溅渣护炉、炉内液态渣固化、添加5±0.5t废钢后,兑入铁水;吹炼脱磷阶段之后、中间倒渣、钢渣碱度按R=CaO/SiO