
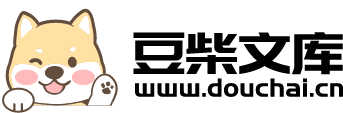
耐磨复合微晶板材.pdf
Th****s3
在线预览结束,喜欢就下载吧,查找使用更方便
相关资料
耐磨复合微晶板材.pdf
本发明涉及对铸石的改性,在铸石的基础上添加一些原料对其加以改进,使之成为一种耐磨复合微晶板材。将天然玄武岩、石英砂、长石、长白石、氮化硼、二硫化钼,按一定重量配比混配均匀,置入晶化炉池炉内升温进行晶化,经充分熔化,水淬为晶化颗粒料;置入热工窑炉中升温,软化、熔融摊平成光滑平整的板材,成为具有坚硬显微结构的多晶烧结体,经退火冷却,研磨及抛光处理,切割成所需规格。本发明是一种高强度、高耐磨、耐腐蚀型的防护材料,由于采用天然无机材料,经过两次高温烧结而成的新型绿色环保耐磨复合微晶板材,其耐磨性可达到普通碳钢的数
微晶玻璃复合板材耐磨性能研究.docx
微晶玻璃复合板材耐磨性能研究微晶玻璃复合板材耐磨性能研究摘要:本文通过对微晶玻璃复合板材的耐磨性能进行研究,分析了板材的表面硬度、耐磨损性能及其影响因素。通过实验方法测定了不同材料组分、表面处理以及不同磨损条件下的板材硬度和耐磨性能,得出了不同变量对板材性能的影响。实验结果表明,在一定条件下,微晶玻璃复合板材具有较好的耐磨性能,可满足不同领域的使用需求。关键词:微晶玻璃;复合板材;耐磨性能;硬度;磨损引言随着工业技术的发展,复合材料在各个领域得到了广泛的应用。微晶玻璃复合板材作为一种新兴的复合材料,具有优
耐磨微晶玻璃板材及其制备方法.pdf
本发明公开了一种耐磨微晶玻璃板材及其制备方法。耐磨微晶玻璃板材的原料是由以下组分按重量份配比而成:钢铁炉渣65~85份,石英砂20~30份,氧化镁6~10份,二氧化钛5~10份,氟化钙1~3份;钢铁炉渣的成份及重量百分比含量为:SiO2?13~20%,FeO?10~15%,CaO?40~50%,MgO?5~10%,Al2O3?2~5%,TFe?10~20%,MnO2~5%,P2O3?0.1~0.5%,MFe?0.5~1.5%。方法包括配料、熔制,水淬,研磨过筛,压制成型、核化晶化、抛磨;其中,熔制是在13
耐磨复合板材.pdf
本发明公开一种耐磨复合板材,属于建筑材料制备技术领域。本发明通过在基材木粉中按一定比例加入特定粒径的铁矿渣、碳黑、牛皮、膨润土、铝酸酯偶联剂、醋酸乙酯、聚十一酰胺以及水泥,从而耐磨性好、强度高、韧性好的耐磨复合板材。
微晶耐磨防腐复合托辊及其生产工艺.pdf
本发明公开了一种微晶耐磨防腐复合托辊及其生产工艺,其特征是托辊材料的成份配比为:30-37%的玄武岩晶化,40-45%的聚丙烯,10-12%的高密度聚乙烯,2-3%的石墨粉,10%的石英砂。材料生产工艺为:将上述材料按比例混合后,送入200℃的挤压筒中,物料在200℃挤压筒中边搅拌边挤压边输送,出筒后称重;称重的物料放入高压成型机中,在20-30MP高压下压制成型,出模后进行机械加工得到所需的工件。本发明材料替换钢作为辊筒材料,有效解决了现有托辊自重大、旋转阻力大、耐磨性差、耐腐蚀性差、使用寿命短的问题。